Electroluminescence Imaging, Electroluminescence (EL), an optical and electrical phenomenon, refers to the state of emitting light in response to an electric current or very strong electrical field passing through the material.
It is of great interest among photovoltaic panel quality tests as it detects serious defects that are invisible to the eye and cannot be detected by thermal imaging. It is performed to detect damages that occur during the manufacturing, assembly or transportation of solar panels on a cell-by-cell basis.
Review Mechanism;
Electroluminescence has the same concept as a light emitting diode (LED). This test, which is an X-ray of the solar panels, enables early detection of existing resistive parts and defects that may cause problems in the future.
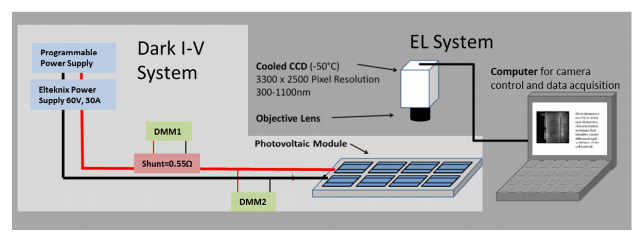
As shown in the image above, a power supply is connected to the solar panel in a closed and dark area, providing the appropriate voltage to reach the short-circuit current. The panel is then photographed with a camera at a fixed distance from the solar panel and the image is then analyzed using a special program.
What defects and problems can we detect with electroluminescence?
- Microfractures
- Production Defects.
- Defects due to Shipment.
- PID.
- Corrosion
- LETID.
The cells produced today are less than 200 micrometers (µm= 1*10-6) thick. These cells are therefore inherently fragile. They must be handled with care and precision.
There are many reasons for micro-fractures in photovoltaic cells.
So what is the cause of these fractures that are invisible to the naked eye?
- The solar panel is in the manufacturing phase;
Micro-fractures can occur in many stages such as cell cutting, cell stringing and soldering processes.
Solar panel manufacturers check with Electroluminescence imaging to detect these cracks in two stages, before and after the lamination process as part of their quality assurance procedures. Based on the inspection results, they classify the panels according to their internal quality standards.
In addition to microfractures, it is also possible to detect other defects. The table below summarizes the most common types of defects.
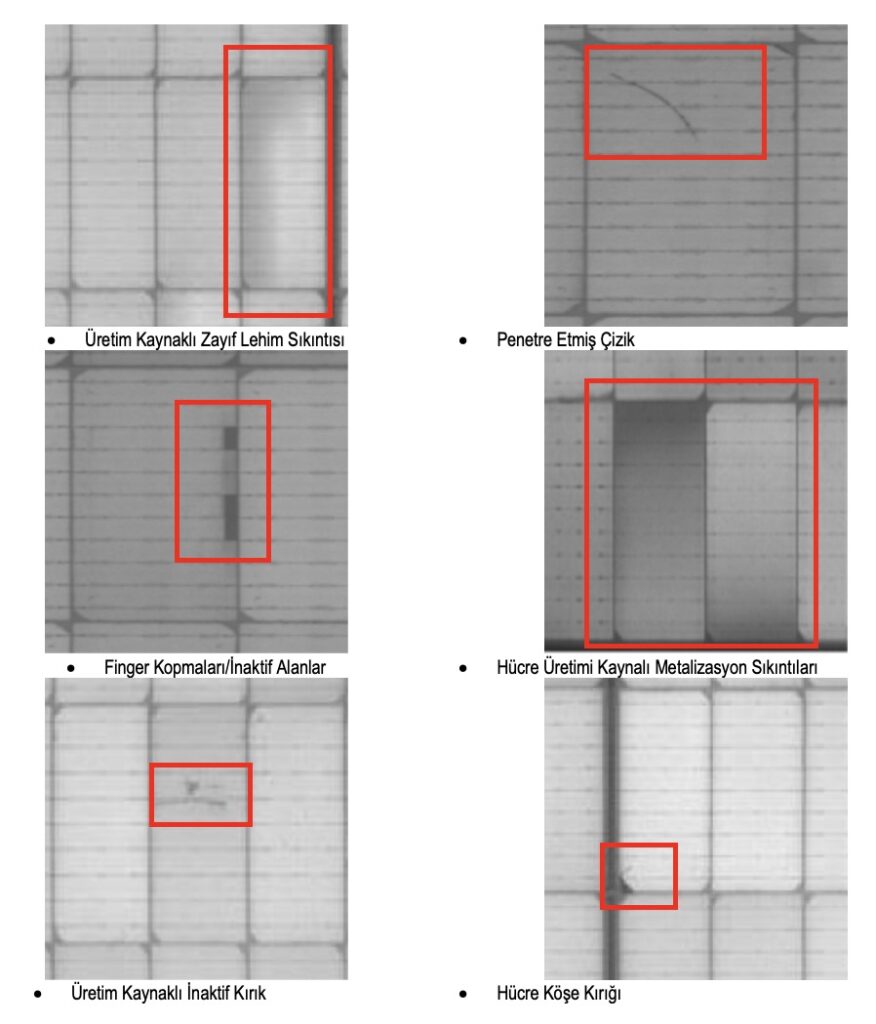
- During shipment and transportation;
Micro-fractures can occur when the panels are shipped from the production factories to the project site. This is because the panels are packed with incorrect packing methods or the instructions in the transportation manual specified by the manufacturer are not followed.
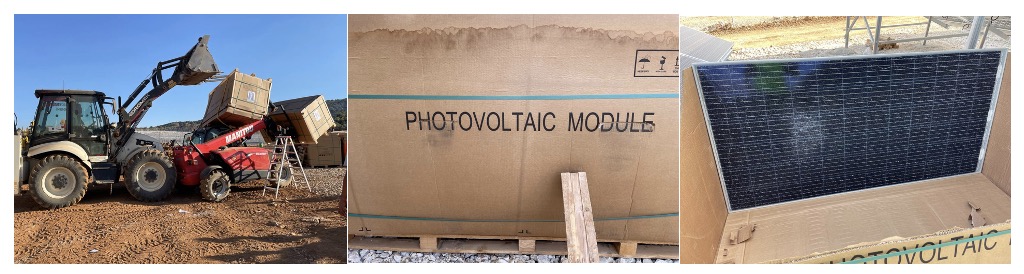
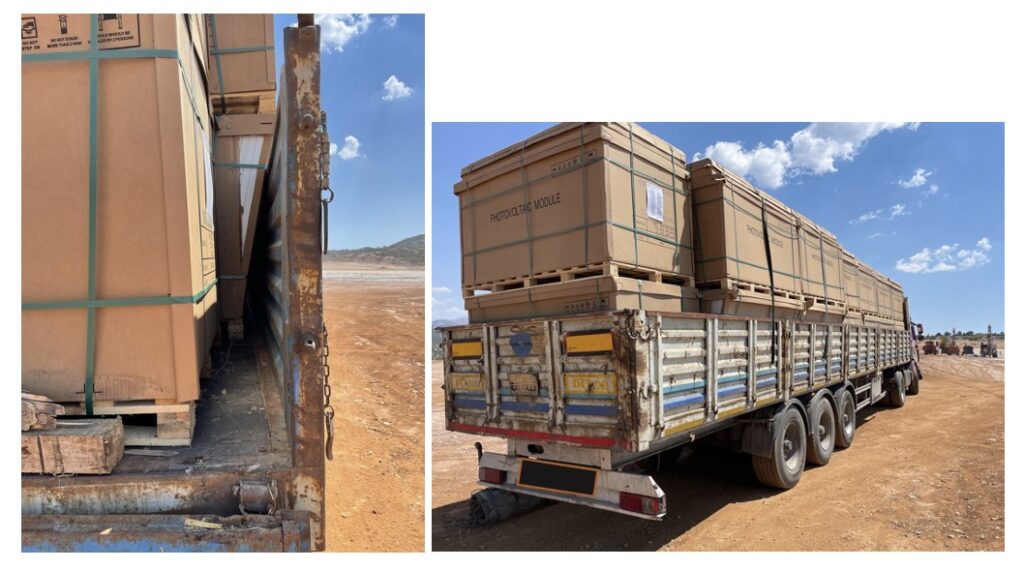
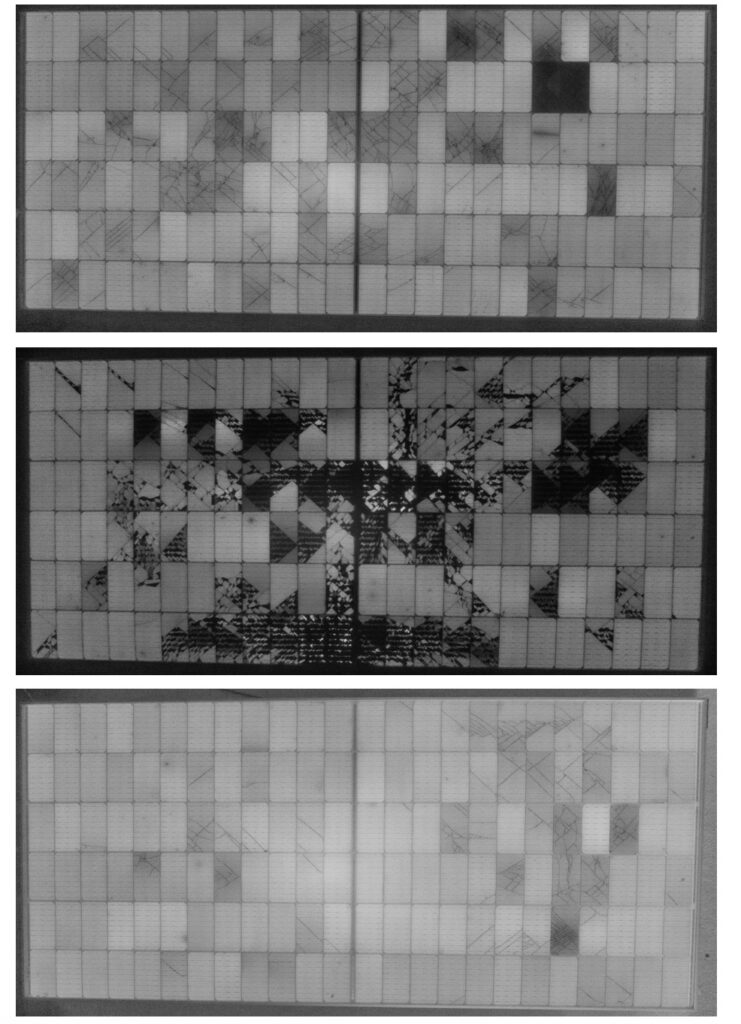
- During the installation phase;
They may occur at the project site during the unloading of panels or during the assembly of panels.
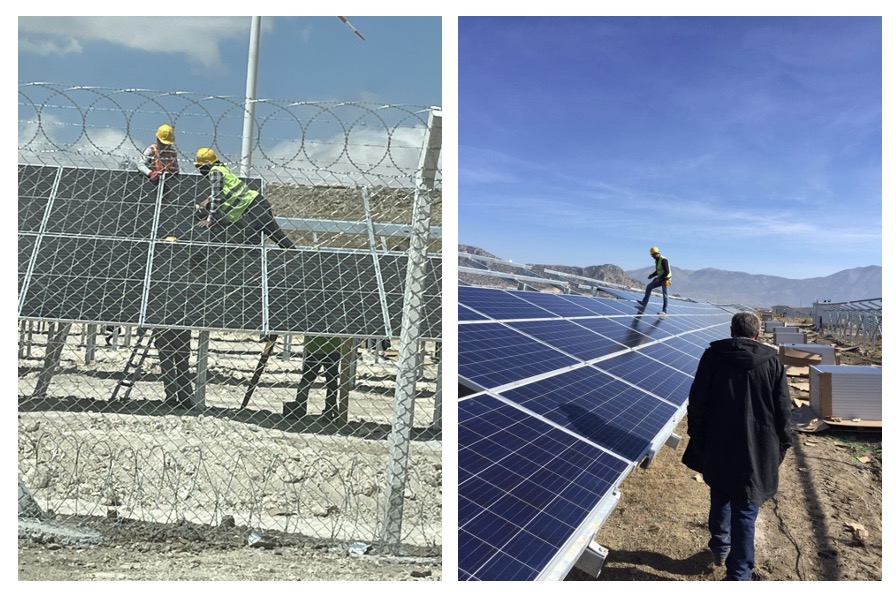
The El images that resulted from the inspection we performed after the installation are as follows. As can be seen, there are many branched/active fractures in the panels that may cause power drop.
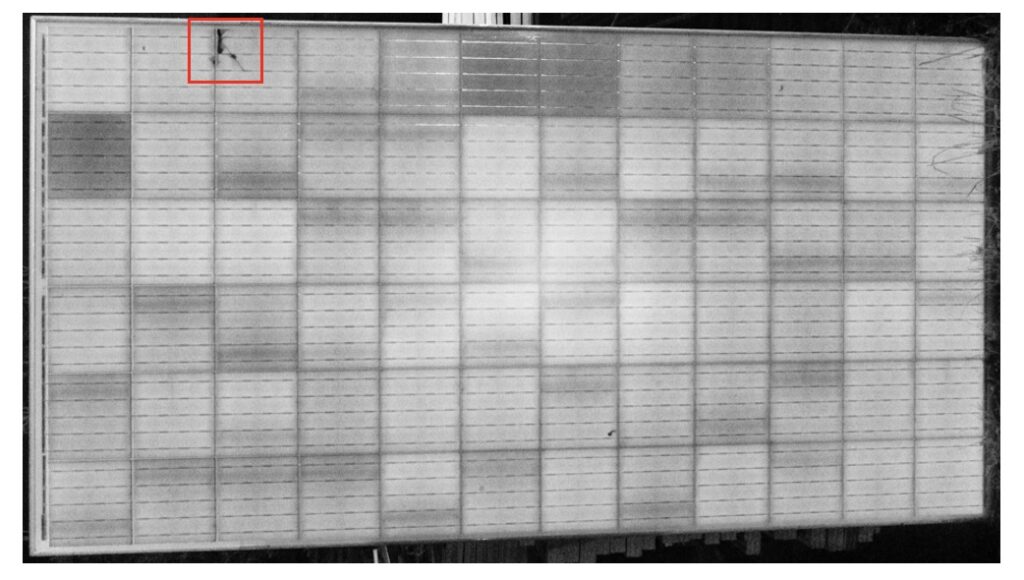

- Maintenance and operation phase;
There are many factors such as the use of inappropriate cleaning methods for the panels, maintenance and operations personnel standing/walking on the panels or other environmental conditions.
- High wind speed.
- Hard falling hail
- Heavy snow load
- Temperature difference between day and night (thermal cycle)
Problems Caused by Micro Fractures
Identifying the problems caused by micro-fractures, the reasons for their occurrence, the impact on the efficiency of the panels or the project as a whole is one of the complex issues in SPP projects, as it depends on many details and technical issues.
From the manufacturer’s perspective, the presence of a micro-fracture in a panel does not necessarily mean that the entire panel is damaged or unsuitable.
Panel manufacturers evaluate panels according to internal quality standards, taking into account the path (shape) and number of micro-fractures, and whether these fractures interfere with the passage of current in some parts of the cell, and whether the damaged parts should be isolated from the photovoltaic cell.
Micro-fractures leading to in-active areas have a direct impact on the production of the cell and therefore on the productivity of an entire panel. In addition, they will cause mismatch losses between arrays (Mismatch Loss).
Micro-fractures that lead to the isolation of part of the cell cause the appearance of Hot Spots, which means that the temperature of the isolated part of the cell rises to high temperatures and
- Backsheet degradation
- Delamination
- Power degradation
will lead to many different problems.
Micro-fractures can expand and propagate depending on the operating conditions of the panels in the field, wind/snow load, mechanical stresses of the panels and panel temperature differences.
Global Standards in Electroluminescence Imaging
- IEC TS 60904-13:2018
Author:
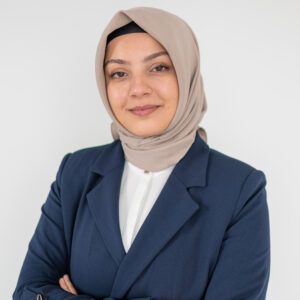