In diesem Artikel werden die Herstellungsverfahren für Photovoltaik-Module (PV-Module), Leistungstests, Qualitätskriterien und Produktionsaudits von Tier-1-PV-Modulherstellern im Solarenergiesektor im Detail besprochen. Die Produktion von PV-Modulen erfordert einen strengen Prozess, um hohe Qualitätsstandards und Leistung zu gewährleisten. Die Produktionsschritte beginnen bei der Auswahl und Aufbereitung des Rohmaterials, über die Zellproduktion, die Modulherstellung und die Modulmontage. In jeder Phase werden regelmäßig Qualitätskontrollen und Leistungstests durchgeführt. Leistungstests sind entscheidend, um die Haltbarkeit, Effizienz und langfristige Leistung von PV-Modulen zu beurteilen. Die Fähigkeit der PV-Module, Sonnenlicht effizient in Strom umzuwandeln, ihre Haltbarkeit und Langlebigkeit bilden die Grundlage der Qualitätskriterien. Diese Hersteller halten sich im Allgemeinen an die besten Praktiken der Branche und hohe Qualitätsstandards. Produktionsprüfungen sind für die Sicherstellung der Qualität und der Einhaltung der Vorschriften unerlässlich. Diese Inspektionen überwachen die Qualität und gewährleisten die Einhaltung der Vorschriften bei jedem Schritt, angefangen bei der Auswahl der Rohstoffe bis hin zur Montage. Die ständigen Entwicklungen in der Solarbranche erfordern eine kontinuierliche Verbesserung der Herstellungsverfahren für PV-Module und der Qualitätsstandards. Die Kombination dieser Elemente trägt wesentlich zur Entwicklung zuverlässiger, effizienter und nachhaltiger PV-Modulsysteme bei.
Was ist eine photovoltaische Zelle?
Die Technologie, die Sonnenenergie in elektrischen Strom umwandelt, heißt Photovoltaik (PV). Die Photovoltaik-Technologie, die Sonnenenergie in nutzbaren Strom umwandelt, erzeugt Elektrizität aus Licht. Halbleitermaterialien, die Sonnenlicht direkt in elektrische Energie umwandeln, werden Photovoltaikzellen genannt. Photonen, die auf die photovoltaische Zelle fallen, verwandeln sich in elektrische Energie. Wenn Sonnenstrahlung auf das Halbleitermaterial fällt, bewegt die Energie der Strahlung die Atome in der äußersten Umlaufbahn der Materialatome. Dieses Ereignis wird als photoelektrisches Ereignis bezeichnet. Durch die Bewegung der losen Atome wird auf Leitern elektrischer Strom erzeugt. Die Elektronen verrichten Arbeit, indem sie die Energie, die sie tragen, an die Hindernisse abgeben, auf die sie treffen. Photovoltaikzellen, die mit Halbleitertechnologie hergestellt werden, basieren auf Silizium. Photovoltaikzellen werden in Reihe und parallel zueinander geschaltet und auf einer Fläche montiert. Dieses zur Erhöhung der Leistung vorbereitete System wird als Photovoltaikmodul bezeichnet. Abbildung 1 zeigt eine Solarzelle, Abbildung 2 ein Solarmodul und ein Solarmodul-Panel [1].
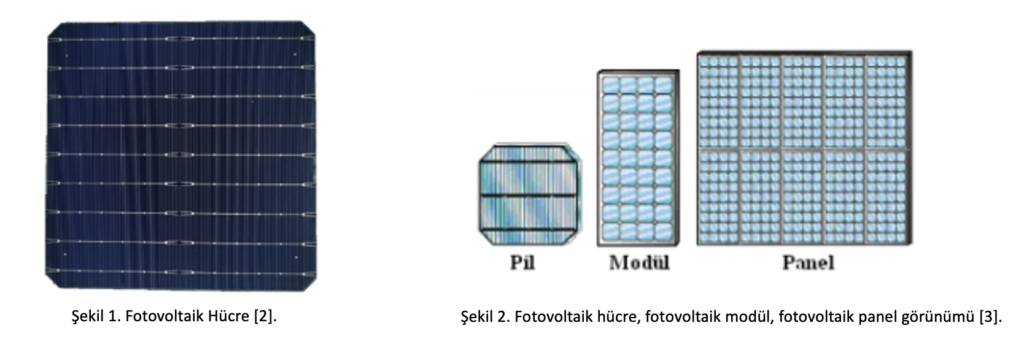
Monokristalline und polykristalline Zelle
Bei dieser Art von Solarzellen werden hochreine Siliziumkristalle als Rohmaterial verwendet. Es gibt zwei Haupttypen: monokristalline und polykristalline Solarzellen.
Ihr Wirkungsgrad ist höher und ihre Lebensdauer länger als bei Zellen, die mit anderen Methoden hergestellt werden.
Die Kristallstrukturen von monokristallinen Photovoltaikzellen mit regelmäßigen Kristallstrukturen sind regelmäßig und daher schwer herzustellen und kostspielig.
Bei polykristallinen Photovoltaikzellen führen sehr geringe Mengen an Defekten in der Kristallstruktur zu einer gewissen Verringerung des Wirkungsgrads solcher Zellen. Die einfache Herstellung und die niedrigen Kosten im Vergleich zu monokristallinen Photovoltaikzellen führen jedoch dazu, dass diese Art von Zellen bei den Konstruktionen immer häufiger eingesetzt wird[4].
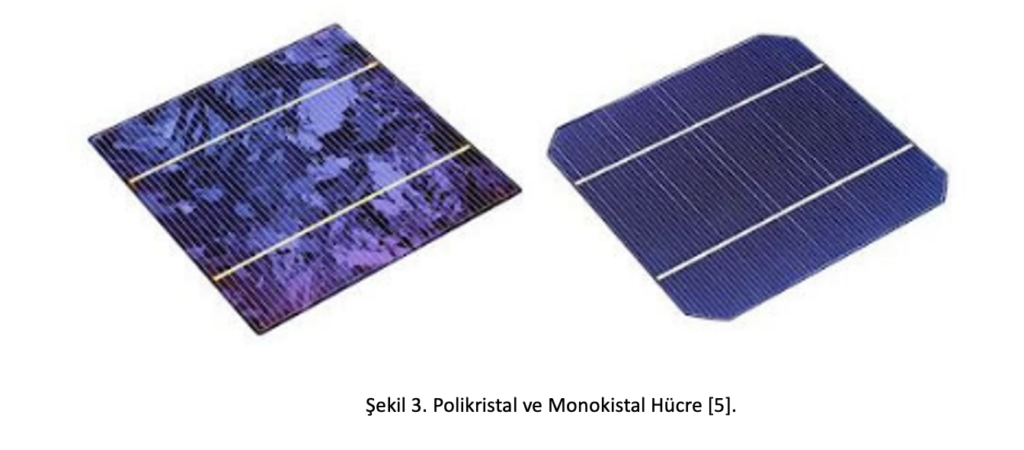
Wie wird ein Photovoltaikmodul hergestellt?
Photovoltaikmodule werden durch die Reihen- oder Parallelschaltung von mono- oder polykristallinen Zellen gebildet, um die gewünschten Strom-, Spannungs- und Leistungswerte zu erreichen. Diese Zellen werden mit Hilfe von Robotern gelötet. Nach dem Löten werden die Zellen auf ein Material namens Ethylen-Vinyl-Acetat (EVA) gelegt, das hohe Schutz- und Absorptionseigenschaften besitzt. EVA wird auf gehärtetes Glas gelegt und schützt die Zellen vor äußeren Einflüssen. Photovoltaikzellen haben EVA sowohl auf der Vorder- als auch auf der Rückseite. Auf der Rückseite wird ein Material namens TEDLAR verwendet, das das Solarmodul vor Faktoren wie UV-Strahlen, hohen Temperaturen und Feuchtigkeit schützt. Die mit EVA und TEDLAR geschützten Zellen werden in speziellen Laminatoren unter hoher Temperatur und Druck zu einem Ganzen verarbeitet. Anschließend wird die Anschlussdose mit den By-Pass-Dioden, die die Abschattungseffekte minimieren, in das Modul eingesetzt. Als Ergebnis all dieser Prozesse wird das Photovoltaikmodul zu einem Stromerzeuger[1].
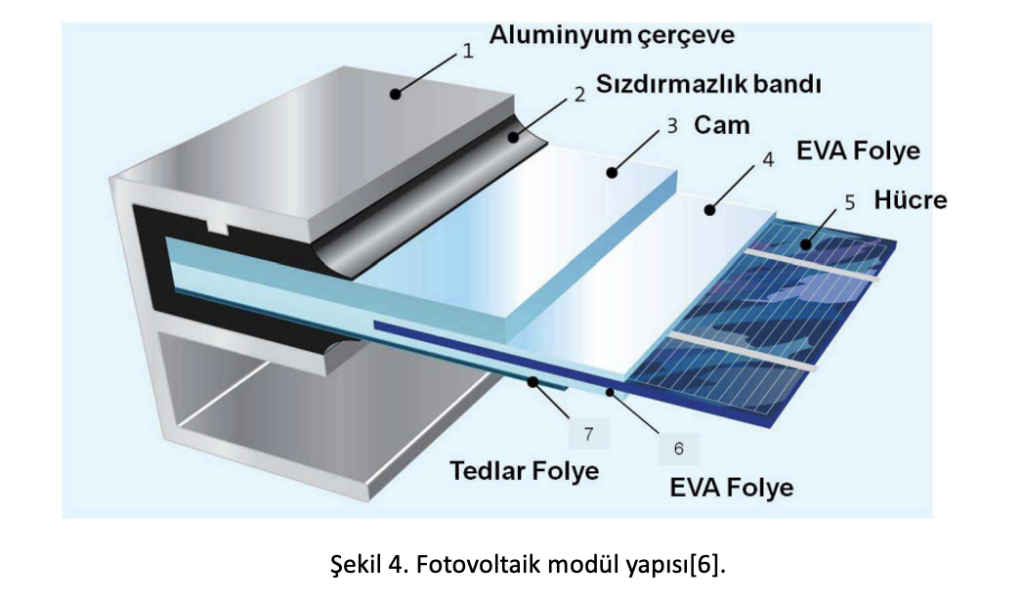
Produktionsstufen von Photovoltaikmodulen
TS EN IEC 61215 Terrestrische Photovoltaik (PV)-Module – Bauartprüfung und Bauartzulassung
Die Norm IEC 61215 legt die IEC-Anforderungen für die Entwurfsqualifikation und die Typenzulassung von terrestrischen Photovoltaikmodulen (PV-Modulen) fest, die für den Langzeitbetrieb in allgemeinen Außenklimata geeignet sind. Diese Norm soll für alle terrestrischen Flachmodulmaterialien gelten, wie z.B. kristalline Siliziummodule und Dünnschichtmodule[7].
TS EN 61730 Sicherheitsmerkmale für Photovoltaik (PV)-Module
IEC 61730 listet die Tests auf, die ein PV-Modul für die Sicherheitsqualifizierung erfüllen muss. IEC 61730-2 und IEC 61730-1 werden zusammen für die Sicherheitsqualifizierung angewendet[8].
Der in dieser Norm festgelegte Prüfablauf prüft möglicherweise nicht alle Sicherheitsaspekte, die bei allen möglichen Anwendungen von PV-Modulen auftreten können. Einige Aspekte, wie z.B. die Gefahr eines Stromschlags durch ein zerbrochenes PV-Modul in einem Hochspannungssystem, müssen durch das Systemdesign, den Standort, die Zugangsbeschränkungen und die Wartungsverfahren berücksichtigt werden [8].
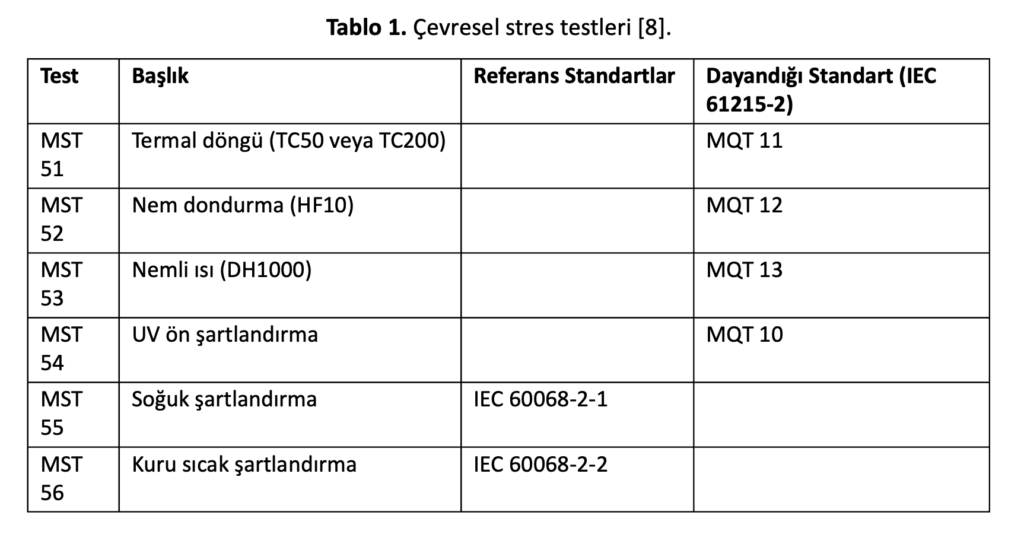
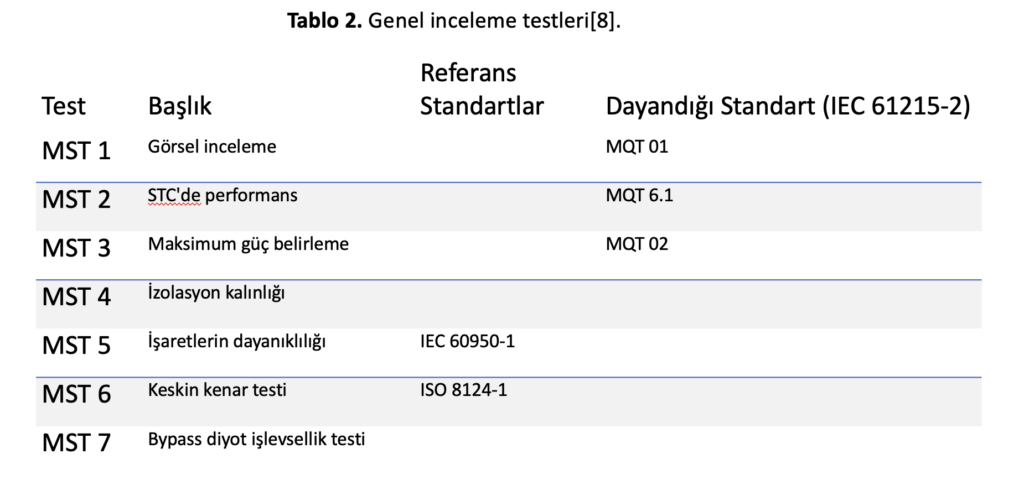
PV-Panel-Fabriken realisieren verschiedene Kombinationen aller Rohstoffe, die für die Panelproduktion verwendet werden sollen, zusammen mit alternativen Marken. Diese Kombinationen, die alle Materialien und speziellen Komponenten enthalten, werden in das Konstruktionsdatenblatt (CDF) aufgenommen. Die Paneele werden gemäß dem CDF hergestellt und zahlreichen Tests unterzogen, wie z.B. dem thermischen Zyklustest, dem Feuchtigkeitsgefriertest, dem feuchten Hitzetest und dem mechanischen Belastungstest, wie in den Normen IEC 61215/IEC61730 gefordert. Solarmodule; Wenn sie die Tests gemäß den Normen IEC 61215 und IEC 61730 erfolgreich bestanden haben, sind sie berechtigt, ein Zertifikat zu erhalten. Nach dieser Phase verfügen die Paneele zusätzlich zum CDF über ein genehmigtes CDF- und IEC 61215/IEC 61730-Zertifikat. Die Fabrik produziert die Paneele gemäß der Materialliste, die BOM List genannt wird, und diese BOM List muss die Materialien im CDF enthalten.
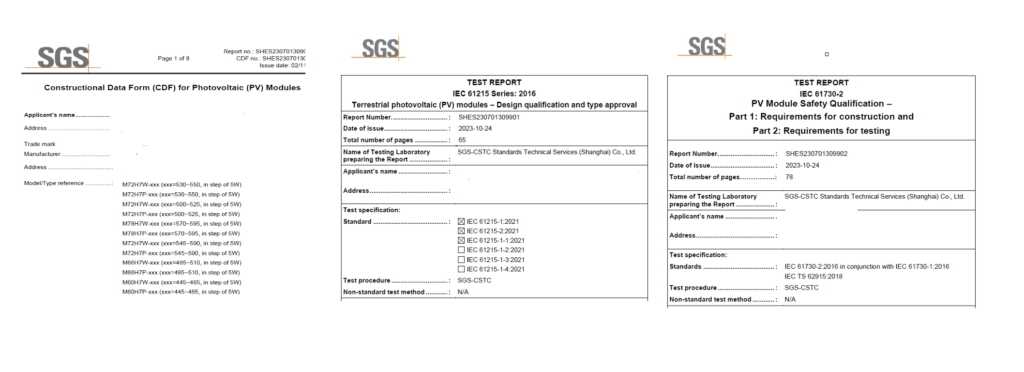
Zelle Test
Das Testen von Solarzellen wird als erstes Verfahren bei der Herstellung von Solarmodulen eingesetzt. Während des Tests wird die elektrische Leistung der Zelle unter einer Sonnensimulation geprüft. Darüber hinaus werden als Qualitätstest unerwünschte negative Effekte wie Oberflächenqualität, Brüche und Risse geprüft [9]. Abbildung 5 zeigt die Zellschneidemaschine.
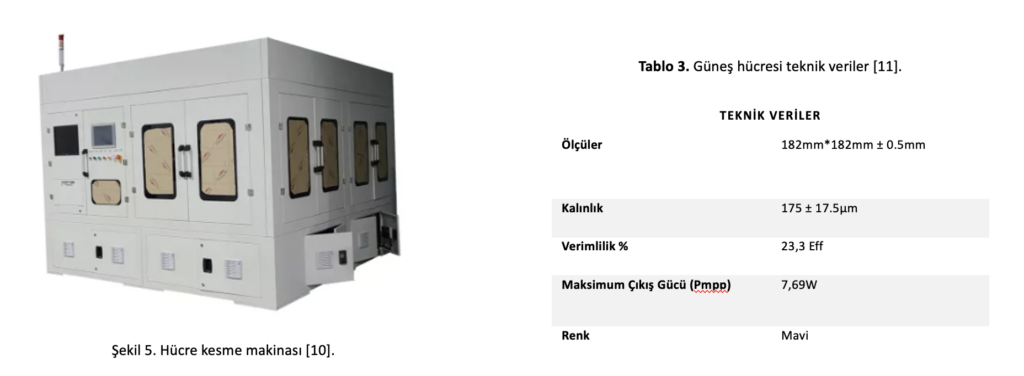
Glas laden
Die bei der Herstellung von Solarmodulen verwendeten Gläser sind flache oder matte, gehärtete Gläser mit geringem Eisenoxidgehalt. Der geringe Eisenoxidgehalt erhöht die Lichtdurchlässigkeit des Glases. In der Produktionslinie werden die Gläser von automatischen Roboterarmen präzise geladen. Die hohe Präzision der Roboterarme minimiert das Risiko von Glasbruch und Rissen während des Ladens. Nachdem die Gläser verladen wurden, werden sie einer Oberflächenkontrolle und Reinigung unterzogen. In diesem Stadium werden Risse und Verformungen auf der Oberfläche erkannt [9]. Abbildung 6 zeigt das Glas eines PV-Moduls und Abbildung 7 zeigt die Glaslademaschine einer Fabrik, die PV-Module herstellt.
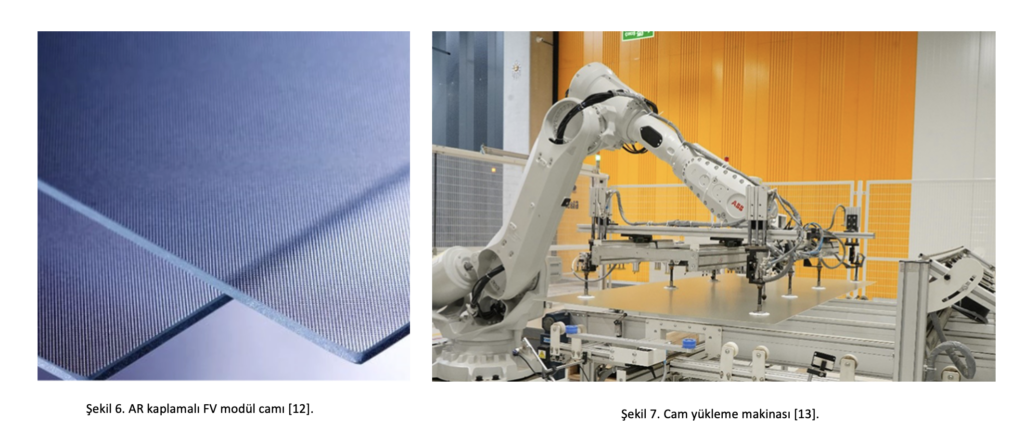
Folienverlegelinie
EVA-Solarfolien (Ethylenvinylacetat) werden in Produktionsanlagen für Solarmodule verwendet, um die Stromerzeugung effizienter zu machen und die Zellen vor Stößen zu schützen. In dieser Produktionslinie werden die EVA-Folien zwischen dem Glas und den Zellen kombiniert [9]. Abbildung 8 zeigt die EVA-Verlegemaschine.
EVA ist eine spezielle Schicht und befindet sich sowohl zwischen dem Glas und den Zellen als auch zwischen den Zellen und der Rückseitenfolie. Das auf beiden Seiten aufgebrachte EVA wird durch Heißlaminierung geschmolzen und umhüllt die Solarzellen vollständig. Dieser Prozess erhöht die Haltbarkeit des Panels und verhindert, dass Elemente wie Wasser und Mikrostaub ins Innere gelangen. Außerdem schützt es die Solarzellen, indem es Stöße und Vibrationen abfängt[14].
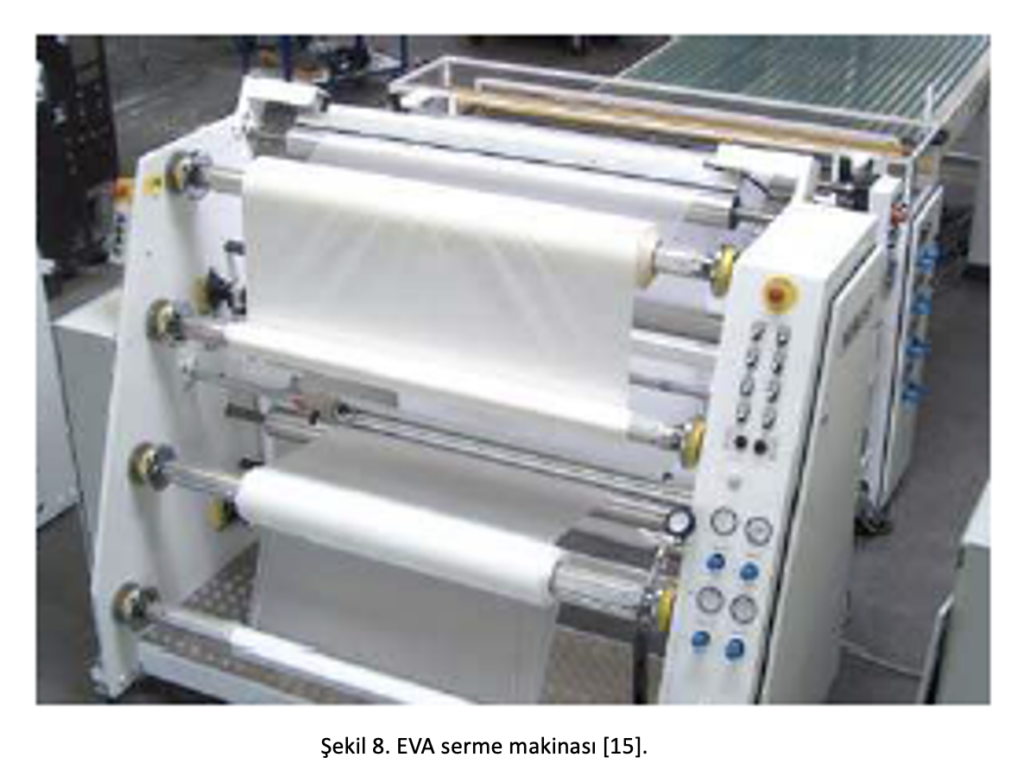
Stringer und Lötkolben
Nachdem die Mikrorisse und Verformungen auf den Solarzellen erkannt wurden, werden die Zellen in der Produktionslinie sorgfältig ausgerichtet. Stringer-Maschinen führen den Lötprozess mittels Infrarot oder Laser durch, nachdem sie Lotpaste auf die Zellen gesprüht haben [9]. Abbildung 9 zeigt die Stringer-Maschine. In der Stringer-Maschine werden leitende Drähte, sogenannte Ribbons, auf die Zellen gelötet. Abbildung 10 zeigt eine Visualisierung des Lötvorgangs.
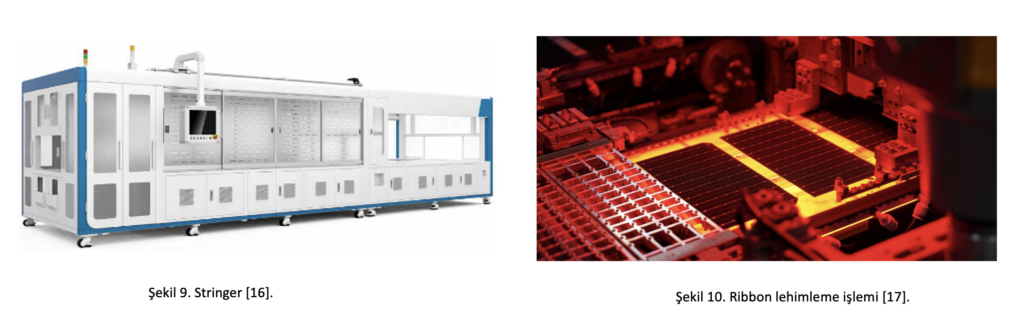
Kaschieranlage
Nachdem das PV-Modul den Stringer-Bereich verlassen hat, wird es zur Laminierungslinie geschickt, indem wieder EVA-Material auf die Rückseite gelegt und entweder AR-beschichtetes Glas oder Backsheet darauf gelegt wird. Hier verschmelzen alle Materialien bei hoher Temperatur und hohem Druck miteinander und werden zu einem Ganzen.
Backsheets sind die äußere Schicht von Solarmodulen und sorgen für die elektrische Isolierung der internen Schaltkreise von der äußeren Umgebung. Diese Schicht spielt eine entscheidende Rolle beim Schutz des Panels vor rauen Umweltbedingungen. Sie erhöht die Haltbarkeit der Solarmodule während ihrer gesamten Lebensdauer und reduziert das Sicherheitsrisiko [14]. Abbildung 11 zeigt die für das PV-Modul verwendete Rückseitenfolie. In der Laminierstraße muss das EVA-Material bei konstanter Zeit und Temperatur vollständig schmelzen, um ein transparentes Aussehen zu erhalten und die Zellen und das gesamte Panel sehr gut zu halten [9]. Abbildung 12 zeigt die Laminierstraße.
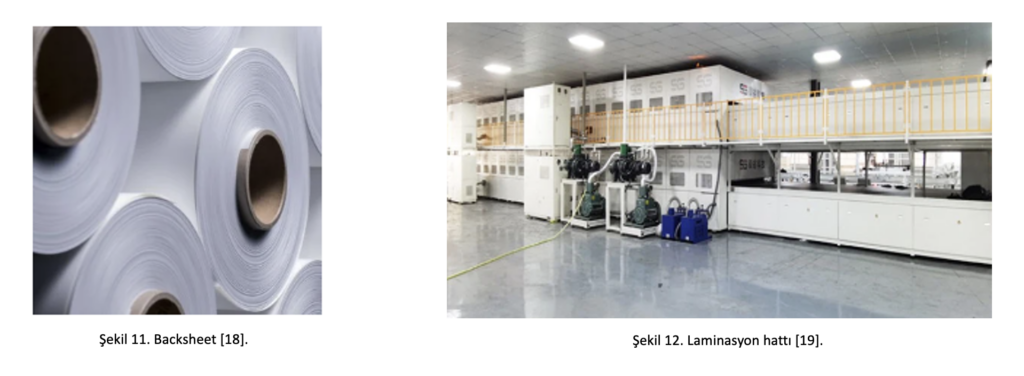
Liniedrücken
Nach dem Besäumen der Kanten und dem Zuschneiden der Paneele und Rahmen werden sie an diese Linie geschickt, um den Rahmen zu montieren. Nachdem der Rahmen fertiggestellt ist, wird der Anschlusskasten an den Paneelen montiert [9]. Abbildung 13 zeigt die Rahmenpresslinie. Aluminiumrahmen, die bei der Herstellung von PV-Modulen verwendet werden, sind wichtige Komponenten, bei denen Faktoren wie die geeignete Gestaltung der Befestigungslöcher, die eingestellten Gewichte, die Beschichtungsdicke und die Anteile der Elemente am Inhalt berücksichtigt werden sollten. Ein niedriger Eisengehalt in Aluminiumrahmen verringert das Korrosionsrisiko und eine Eloxalbeschichtung verhindert das Anlaufen [14]. Der Rahmen ist in Abbildung 14 dargestellt.
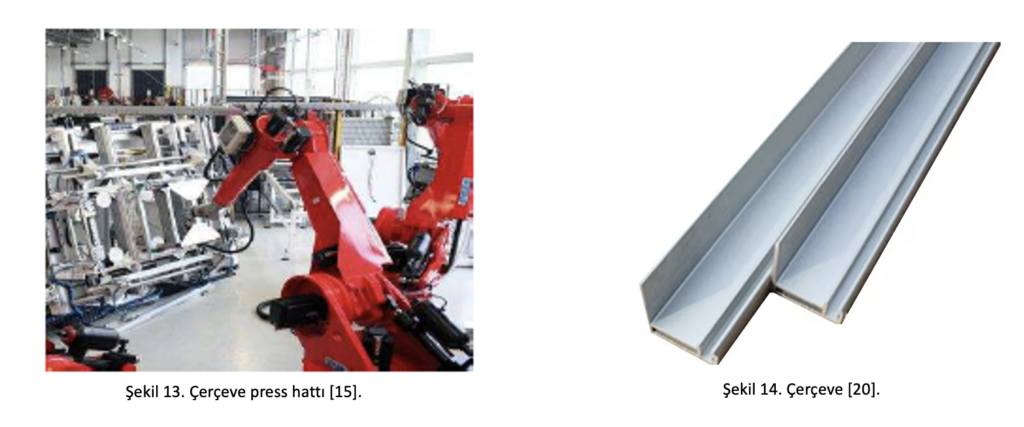
Verteilerdose Verbinden
An den Modulen, die aus dem Rahmen kommen, ist eine Anschlussdose angebracht. Die Anschlussdose, die die Zellen in Photovoltaik-Solarmodulen in Reihe miteinander verbindet, schützt das Modul elektrisch, indem sie den erzeugten Strom an die externen Leitungen weiterleitet. Die Dioden im Inneren bieten Schutz vor den UV-Strahlen der Sonne. Gleichzeitig bietet diese Box Zugang zur Erkennung und Reparatur von Fehlfunktionen, die im Panel auftreten können [14]. Abbildung 15 zeigt die Anschlussbox.
Die Rohstoffkontrollen, die während des Produktionsaudits durchgeführt werden, sollten auch für Backsheet, Anschlussdose und Rahmen durchgeführt werden. Dabei ist zu beachten, dass die Markenmodelle dieser Produkte in der CDF enthalten sind. Wenn wir diese Frage speziell für die Anschlussdose betrachten, gibt es drei Punkte, die überprüft werden müssen. Das sind die Bypass-Wahl, das Kabel und der Anschluss. Diese drei Elemente bilden die Anschlussdose. Jede Marke von Anschlussdosen kann unterschiedliche Produkte für diese drei Elemente verwenden. So wird beispielsweise eine Bypass-Diode mit der Codierung 4045 in einer Anschlussdose mit einem Nennstrom von 25 A verwendet, während 5045 für 30 A eingesetzt werden kann. Auch diese Kombinationen müssen der CDF entsprechen.
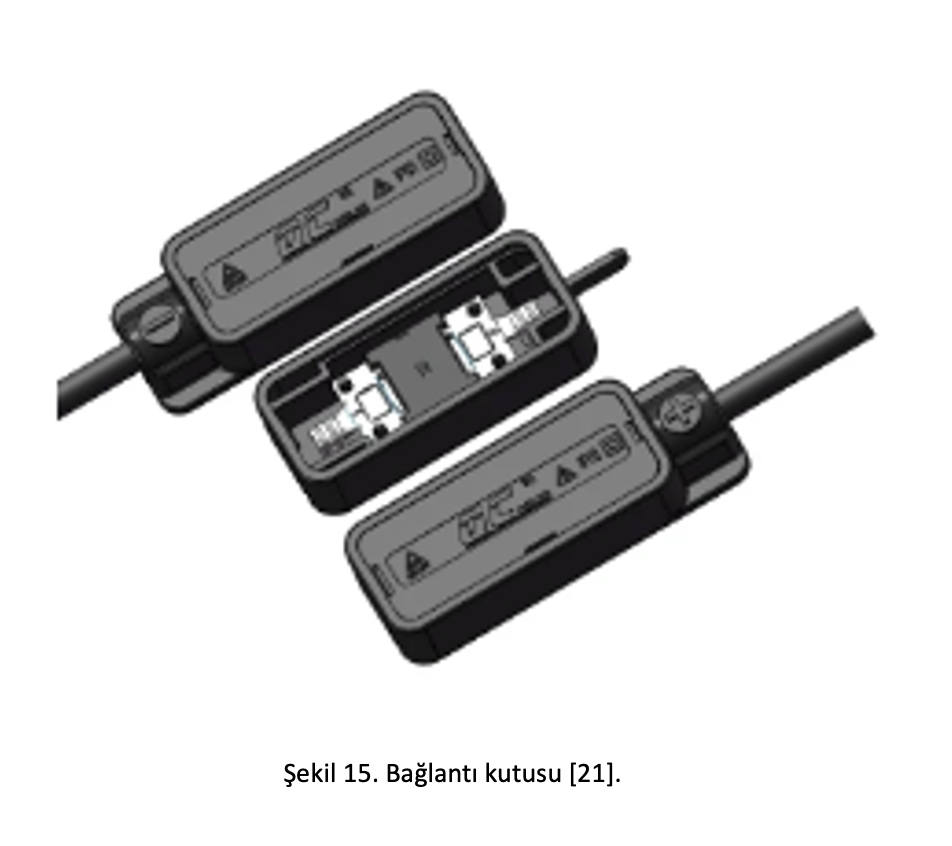
Im Rahmen von IEC 61215/IEC 61730 angewandte Tests
Visuelle Inspektion
Die PV-Module werden unter einer Beleuchtung von mindestens 1000 Lux auf die folgenden Bedingungen geprüft.
-Rissige, verzogene, falsch ausgerichtete oder gerissene Außenflächen
-Zerbrochene, rissige Zellen,
-Fehlerhafte Verbindungspunkte oder Verbindungen,
-Zellen in Kontakt miteinander oder mit dem Rahmen,
-Störung der Klebeverbindungen,
-Ein kontinuierlicher Pfad zwischen einer Zelle und dem Rand eines Moduls, der durch Blasen oder Falten gebildet wird,
-Verbundene Oberflächen von Kunststoffen,
-Fehlerhafte Anschlüsse, die stromführenden Teilen ausgesetzt sind,
-alle anderen Bedingungen, die die Leistung beeinträchtigen können [22].
Elektrolumineszenz (EL) Bilder von PV-Modulen werden analysiert, um Mikrobrüche zu erkennen, die mit dem Auge nicht sichtbar sind.
Elektrolumineszenzbilder werden in der Regel in schwach beleuchteten Umgebungen aufgenommen und sind in der Regel in Graustufen gehalten. Defekte in solchen Bildern erscheinen in der Regel in dunklen Regionen; insbesondere erscheinen Brüche und andere Defekte als schwarze Linien oder dunkle Flecken. Die Elektrolumineszenz-Bildgebung ist eine weit verbreitete Methode zur Fehlererkennung in vielen Fertigungsbetrieben [23]. Abbildung 16 zeigt das EL-Bild des PV-Moduls.
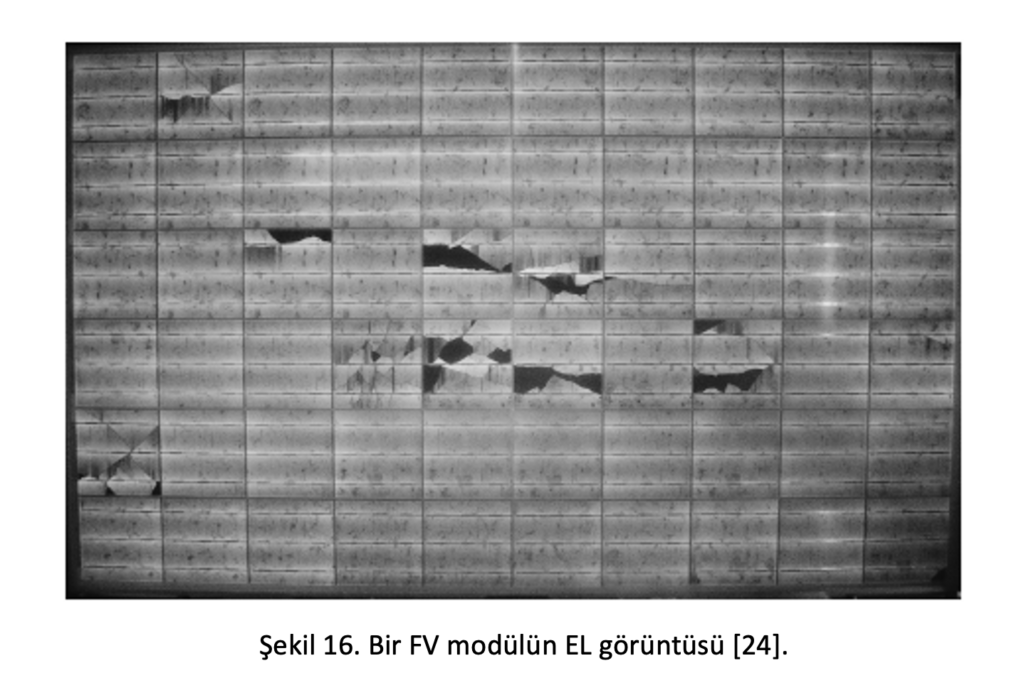
Bestimmung der maximalen Leistung ( Bestimmung dermaximalen Leistung )
Die Leistung des PV-Moduls wird bei einer Bestrahlungsstärke von 1000W/m² und einer Temperatur von 25°C bestimmt[22].
Isolationstest
Mit dieser Prüfung wird festgestellt, ob eine gute Isolierung zwischen den stromführenden Teilen des Moduls und dem Rahmen oder der Umgebung gegeben ist. Der Isolationswiderstand von Modulen mit einer Fläche von weniger als 0,1m2 darf nicht weniger als 400 MΩ betragen. Bei Modulen mit einer Fläche von mehr als 0,1m2 darf der Wert des Isolationswiderstands, gemessen bei 500 V oder der maximalen Systemspannung, je nachdem, welcher Wert größer ist, multipliziert mit der Modulfläche, nicht weniger als 400 MΩ xm2 betragen [22]. Abbildung 17 zeigt den TSE-Isolationsprüfschrank.
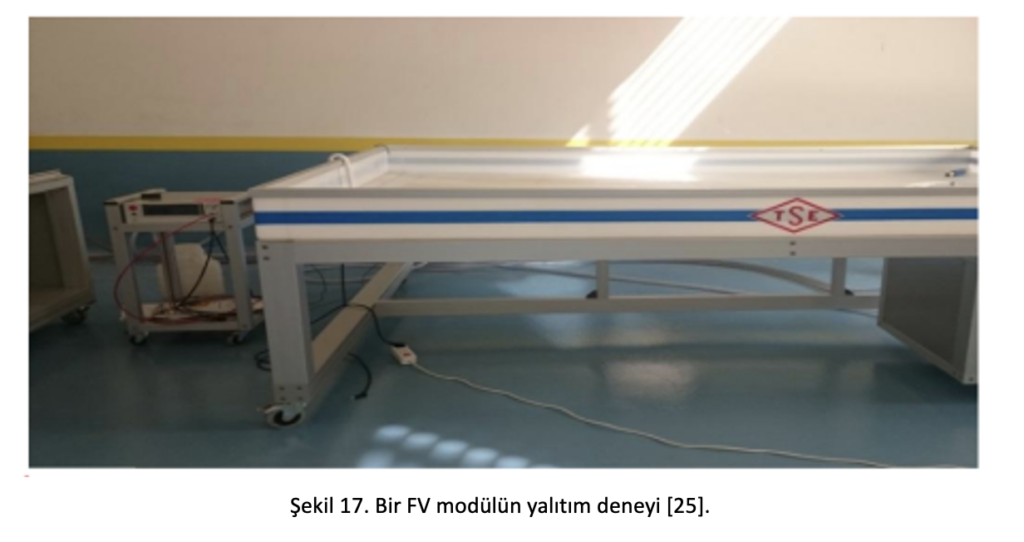
Messung der Temperatur Koeffizienten
Die Leistung von monokristallinen und polykristallinen Zellen mit Kristalltechnologie nimmt mit steigender Temperatur ab. Der niedrige Temperaturkoeffizient verringert den Energieverlust, wenn die Temperatur steigt. Wenn das Modul die gewünschte Temperatur erreicht, werdenISC, VOC und Spitzenleistung gemessen. Die Modultemperatur wird in Schritten von etwa 5°C über den interessierenden Bereich von mindestens 30°C geändert und die Messungen vonISC, VOC und Spitzenleistung werden wiederholt [22]. Abbildung 18 zeigt das entsprechende Experiment.
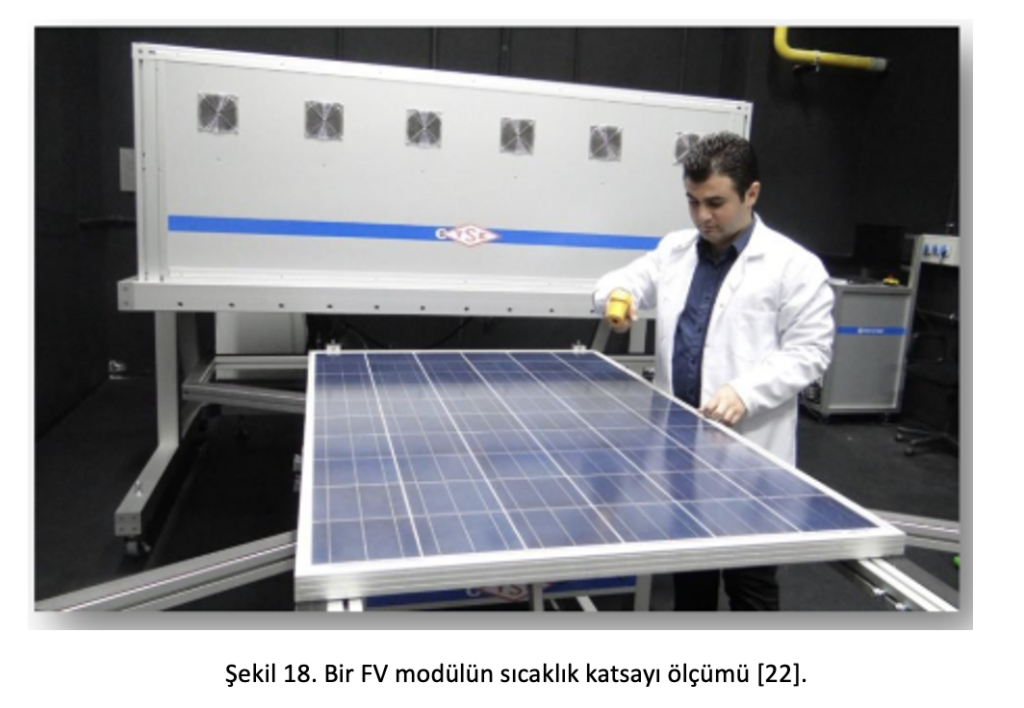
Hot-Spot Dauertest
Der Zweck dieses Experiments ist es, die Fähigkeit des Moduls zu bestimmen, Hot-Spot-Erwärmungseffekten standzuhalten, z.B. kann das Schmelzen des Lots oder die Verformung des Gehäuses einen Erwärmungseffekt erzeugen. Dieser Defekt kann auch durch gerissene oder nicht zusammenpassende Zellen, zusammengeschaltete Defekte, partielle Geisterbilder oder Makel verstärkt werden. Es sollten keine sichtbaren Defekte vorhanden sein, die Verringerung der maximalen Ausgangsleistung sollte 5% des vor dem Test gemessenen Wertes nicht überschreiten und der Isolationswiderstand sollte den ursprünglichen Messungen entsprechen[22].
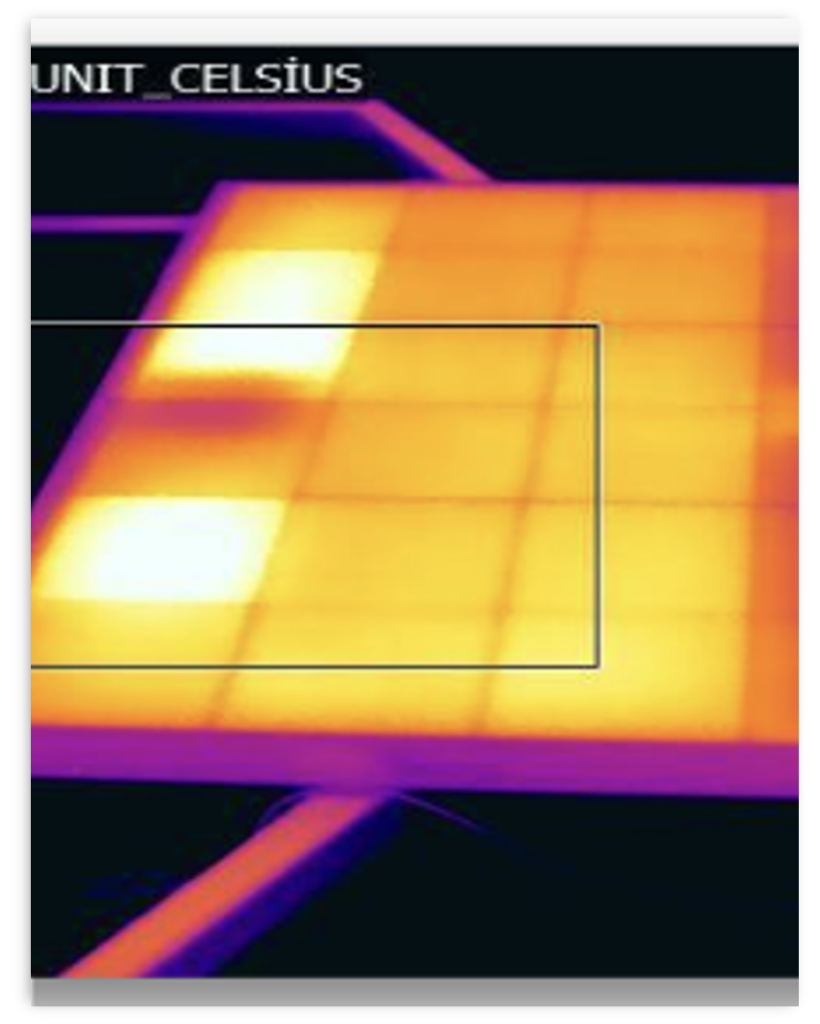
Ultravioletter Vorkonditionierungstest
Das PV-Modul wird mit ultravioletter (UV) Strahlung vorkonditioniert, um Materialien und Klebebinder zu identifizieren, die vor den Experimenten zum thermischen Zyklus/Feuchtigkeitsgefrieren empfindlich auf UV-Abbau reagieren. Das Modul wird bei einer Temperatur von 60 ºC ± 5 ºC mit einem Wellenlängenbereich zwischen 280 nm und 385 nm mit insgesamt 15 kWh/m2 bestrahlt,während es mit UV-Licht bestrahlt wird. [22].
Thermischer Zyklustest (Thermischer Zyklustest)
Es wird die Fähigkeit des PV-Moduls ermittelt, thermischer Fehlanpassung, Ermüdung und anderen durch wiederholte Temperaturänderungen verursachten Belastungen standzuhalten. Es werden 50 und 200 Zyklen in einem Bereich von -40 °C bis +85 °C durchgeführt. Während des Experiments sollte der Stromfluss nicht unterbrochen werden[22].
Luftfeuchtigkeits-Frost-Test
Er bestimmt die Fähigkeit des PV-Moduls, hohen Temperatur- und Feuchtigkeitseinflüssen nach Temperaturen unter dem Gefrierpunkt standzuhalten. Es handelt sich nicht um einen Thermoschocktest. 10 Zyklen werden bei +85 °C und -40 °C und 85% relativer Luftfeuchtigkeit durchgeführt [22].
Feuchte-Wärme-Test
Er bestimmt die Fähigkeit des PV-Moduls, Feuchtigkeit und langfristigen Eindringungseffekten zu widerstehen. Der Test dauert 1000 Stunden bei +85 °C und 85% relativer Luftfeuchtigkeit[22].
Nasser Leckstromtest (Nass Leckstrom Stromtest)
Dieser Test bewertet die Isolierung des PV-Moduls unter nassen Betriebsbedingungen und stellt sicher, dass Feuchtigkeit aus Regen, Nebel, Tau oder geschmolzenem Schnee nicht in die aktiven Teile des Modulstromkreises eindringt und Korrosion, Erdschluss oder Sicherheitsrisiken verursacht[22].
-Widerstand: 3.500Ω oder weniger
-Oberflächenspannung: 0,03 N/m oder weniger
-Temperatur: 22 ºC ± 3 ºC
Bei Modulen mit einer Fläche von weniger als -0,1 m² sollte der Isolationswiderstand nicht weniger als 400 MΩ betragen. Bei Modulen mit einer Fläche größer als 0,1 m² sollte der gemessene Isolationswiderstand multipliziert mit der Fläche des Moduls nicht weniger als 40 MΩ.m² betragen [22].
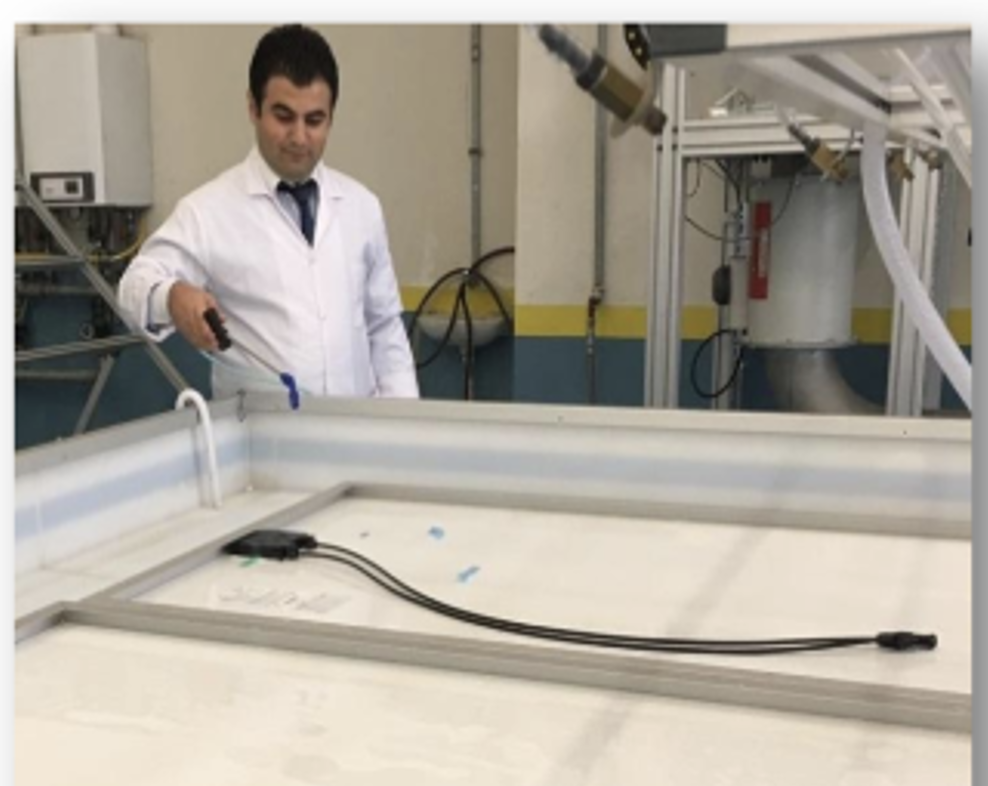
Mechanischer Belastungstest (Mechanischer Belastungstest)
Der Zweck dieses Experiments ist es, den Widerstand eines Photovoltaik-Moduls (PV) gegen Wind, Land, statische Lasten oder Eislasten zu bestimmen. Während des Experiments wird das Modul gespeist, um die elektrische Integrität der internen Schaltkreise des Moduls kontinuierlich zu überwachen. Eine Last von 2400 Pa wird 1 Stunde lang für drei Zyklen auf die Vorder- und Rückseite des Moduls aufgebracht[22].
2400 Pa gilt als Referenz für starke Winde mit einem Sicherheitsfaktor von 3 und einer Geschwindigkeit von 130 km/h (ca. ± 800 Pa). Wenn das Modul starken Schnee- oder Eisansammlungen standhalten muss, wird die auf die Vorderseite des Moduls auszuübende Kraft für den letzten Zyklus von 2400 Pa auf 5400 Pa erhöht. Während des Tests sollte kein kontinuierlicher Unterbrechungsfehler festgestellt werden und es sollten keine größeren sichtbaren Defekte vorhanden sein. Außerdem sollte die Reduzierung der maximalen Ausgangsleistung nicht mehr als 5% des vor dem Experiment gemessenen Wertes betragen [22].
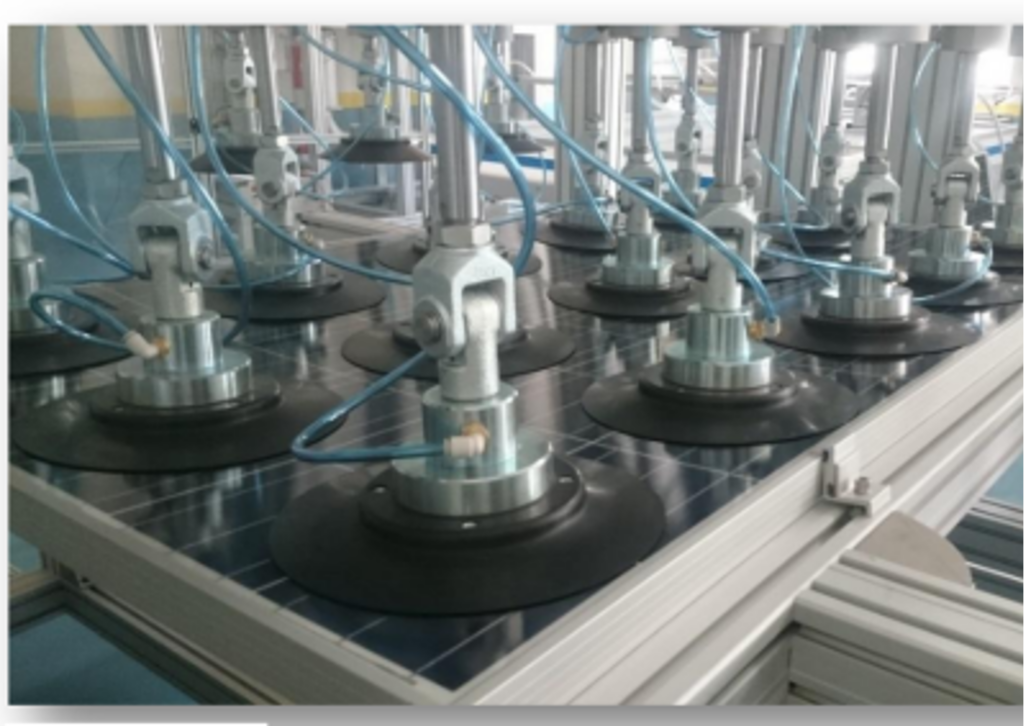
Elektrolumineszenz (EL) Bildgebung
Die frühzeitige Erkennung von Defekten in Photovoltaikmodulen ist entscheidend, um die Effizienz, Zuverlässigkeit und Langlebigkeit der Systeme zu gewährleisten. Defekte können die Effizienz der Panels verringern, die Energieproduktion einschränken und Sicherheitsrisiken darstellen. Diese Erkennungen erfolgen durch Methoden wie visuelle Inspektion, elektrische Tests und Leistungsüberwachung und werden von spezialisierten Teams durchgeführt. Insbesondere die Elektrolumineszenz (EL)-Bildgebung ist eine weit verbreitete Methode, um Brüche und andere Defekte in Paneelen zu erkennen. EL-Geräte erkennen Defekte, indem sie die Strahlung, die durch die an die Paneele angelegte Gleichspannung erzeugt wird, mit speziellen Kameras auffangen. Dieser Prozess ist notwendig, um die Leistung und Lebensdauer der Paneele während der Produktions- und Betriebsphase zu verbessern, und muss den lokalen Vorschriften entsprechen. Die Erkennung und Beseitigung von Defekten gewährleistet eine optimale Leistung des Systems, reduziert die Betriebskosten und erhöht den Nutzen für die Umwelt [23].

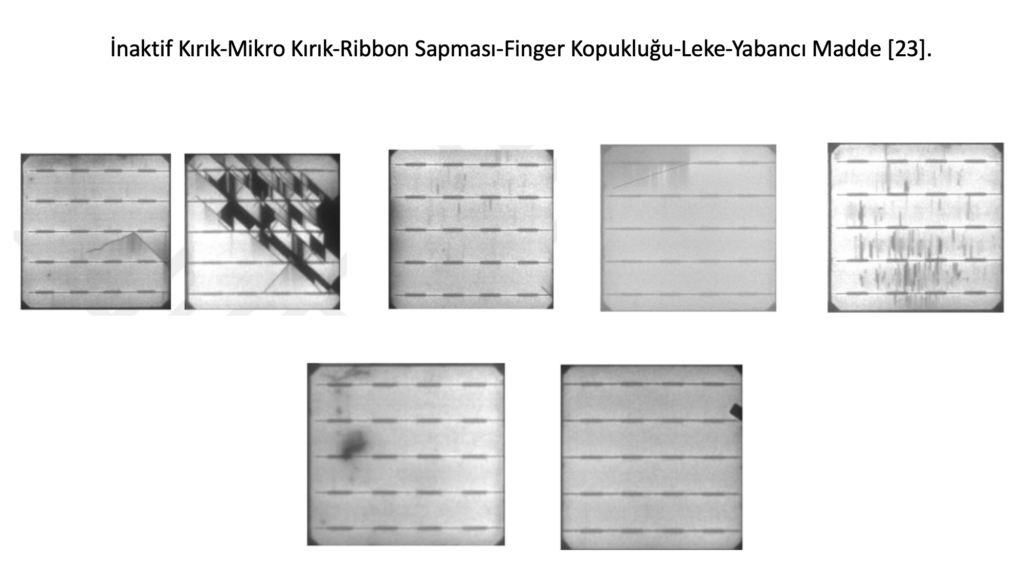
Autor:
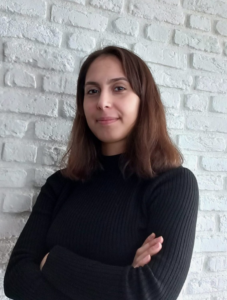
Melisa Ekşi