Este artículo analiza en detalle los procesos de fabricación de módulos fotovoltaicos (FV), las pruebas de rendimiento, los criterios de calidad y las auditorías de producción de los fabricantes de módulos FV de primer nivel en el sector de la energía solar. La producción de módulos fotovoltaicos requiere un proceso riguroso para garantizar unos niveles de calidad y rendimiento elevados. Las fases de producción comienzan con la selección y preparación de las materias primas, pasando por la producción de células, la construcción de módulos y el montaje de los mismos. En cada etapa se realizan regularmente pruebas de control de calidad y de rendimiento. Las pruebas de rendimiento son fundamentales para evaluar la durabilidad, la eficiencia y el rendimiento a largo plazo de los módulos fotovoltaicos. La capacidad de los módulos FV para convertir eficazmente la luz solar en electricidad, su durabilidad y longevidad constituyen la base de los criterios de calidad. Por lo general, estos fabricantes se adhieren a las mejores prácticas de la industria y a normas de alta calidad. Las auditorías de producción son vitales para garantizar la calidad y la conformidad. Estas inspecciones controlan la calidad y garantizan el cumplimiento en cada paso, desde la selección de las materias primas hasta la fase de montaje. La continua evolución de la industria solar exige una mejora continua de los procesos de fabricación de módulos fotovoltaicos y de las normas de calidad. La combinación de estos elementos contribuye significativamente al desarrollo de sistemas de módulos FV fiables, eficientes y sostenibles.
¿Qué es una célula fotovoltaica?
La tecnología que convierte la energía solar en corriente eléctrica se denomina fotovoltaica (FV). La tecnología fotovoltaica, que convierte la energía solar en energía utilizable, genera electricidad a partir de la luz. Los materiales semiconductores que convierten la luz solar directamente en energía eléctrica se denominan células fotovoltaicas. Los fotones que caen sobre la célula fotovoltaica se transforman en energía eléctrica. Cuando la radiación solar incide sobre el material semiconductor, la energía de la radiación mueve los átomos en la órbita más externa de los átomos del material. Este suceso se denomina suceso fotoeléctrico. Con el movimiento de los átomos sueltos, se genera corriente eléctrica en los conductores. Los electrones realizan un trabajo dejando la cantidad de energía que transportan en los obstáculos que encuentran. Las células fotovoltaicas producidas con tecnología de semiconductores se basan en el silicio. Las células fotovoltaicas se conectan en serie y en paralelo entre sí y se montan sobre una superficie. Este sistema preparado para aumentar la potencia de salida se denomina módulo fotovoltaico. La figura 1 muestra la célula fotovoltaica, la figura 2 muestra el módulo fotovoltaico y el panel fotovoltaico [1].
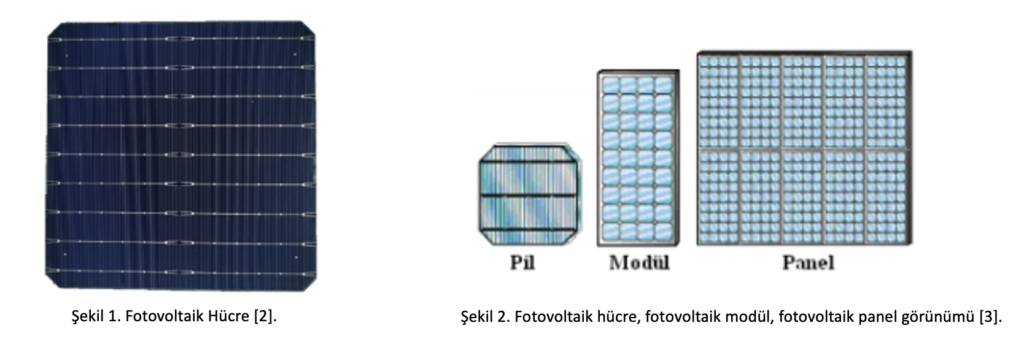
Célula monocristalina y policristalina
En este tipo de células fotovoltaicas se utilizan como materia prima cristales de silicio de gran pureza. Existen dos tipos principales como células fotovoltaicas monocristalinas y policristalinas.
Su eficiencia es mayor y su vida útil es más larga que la de las células producidas por otros métodos.
Las estructuras cristalinas de las células fotovoltaicas monocristalinas son regulares y, por tanto, difíciles de producir y costosas.
En las células fotovoltaicas policristalinas, cantidades muy pequeñas de defectos en la estructura cristalina provocan cierta disminución de la eficiencia de dichas células. Sin embargo, la facilidad de producción y el bajo coste en comparación con las células fotovoltaicas monocristalinas provocan un aumento de la tendencia hacia este tipo de células en los diseños[4].
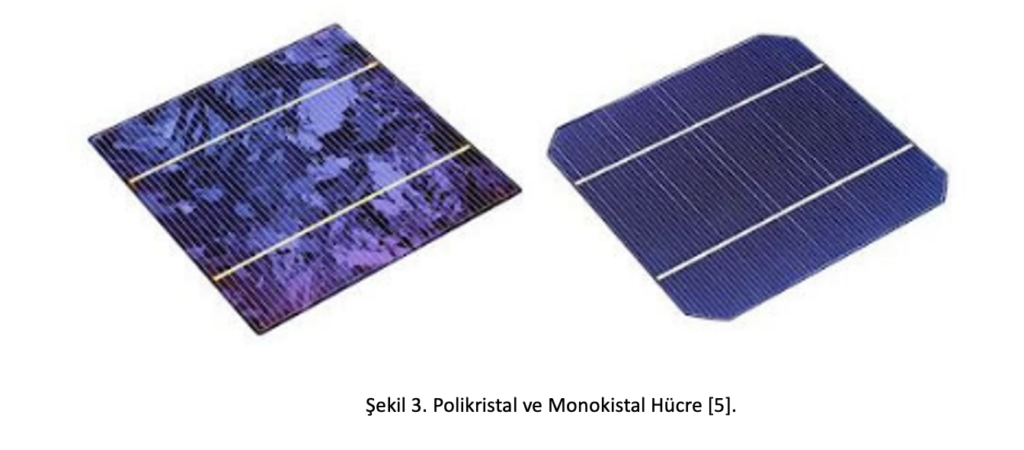
¿Cómo se forma un módulo fotovoltaico?
Los módulos fotovoltaicos se forman conectando células monocristalinas o policristalinas en serie o en paralelo para conseguir los valores de corriente, tensión y potencia deseados. Estas células se sueldan con ayuda de robots. Tras la soldadura, las células se colocan sobre un material llamado etilvinilacetato (EVA), que tiene altas propiedades protectoras y de absorción. El EVA se coloca sobre vidrio templado y protege las células de los factores externos. Las células fotovoltaicas tienen EVA tanto en la superficie delantera como en la trasera. En la cara posterior, se utiliza un material llamado TEDLAR, que protege el panel solar contra factores como los rayos UV, las altas temperaturas y la humedad. Las células protegidas con EVA y TEDLAR se procesan en laminadoras especiales a alta temperatura y presión para formar un todo único. A continuación, se coloca en el módulo la caja de conexiones que contiene los diodos By-Pass, que minimizan los efectos de sombra. Como resultado de todos estos procesos, el módulo fotovoltaico se convierte en un generador de energía[1].
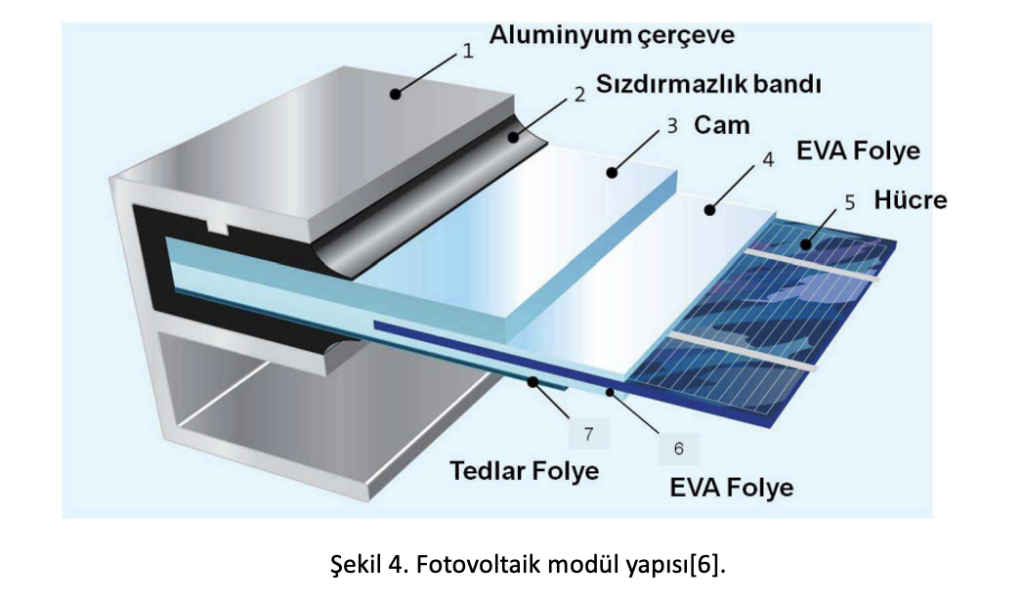
Fases de la producción de módulos fotovoltaicos
TS EN IEC 61215 Módulos fotovoltaicos (FV) terrestres – Cualificación del diseño y homologación
La norma IEC 61215 establece los requisitos de la CEI para la cualificación del diseño y la homologación de módulos fotovoltaicos (FV) terrestres adecuados para un funcionamiento a largo plazo en climas exteriores generales. Esta norma está pensada para aplicarse a todos los materiales de los módulos planos terrestres, como los tipos de módulos de silicio cristalino y los módulos de capa fina[7].
TS EN 61730 Característica de seguridad de los módulos fotovoltaicos (FV)
La norma IEC 61730 enumera las pruebas que debe cumplir un módulo fotovoltaico para obtener la cualificación de seguridad. Las normas IEC 61730-2 e IEC 61730-1 se aplican conjuntamente para la cualificación de seguridad[8].
La secuencia de pruebas especificada en esta norma puede no probar todos los aspectos de seguridad que pueden encontrarse en todas las aplicaciones posibles de los módulos FV. Algunas cuestiones, como el peligro de descarga eléctrica que supone un módulo FV roto en un sistema de alta tensión, deben abordarse mediante el diseño del sistema, la ubicación, las restricciones de acceso y los procedimientos de mantenimiento [8].
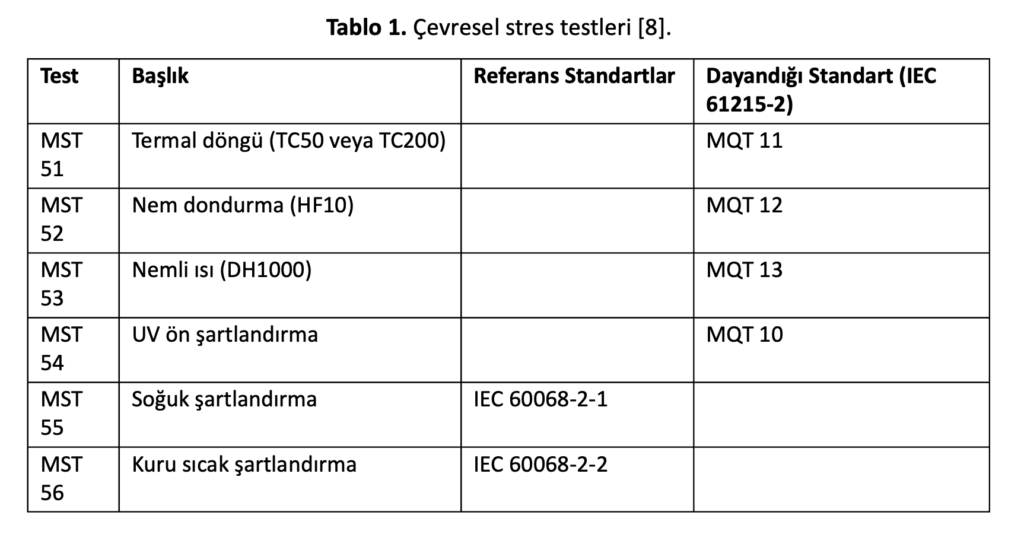
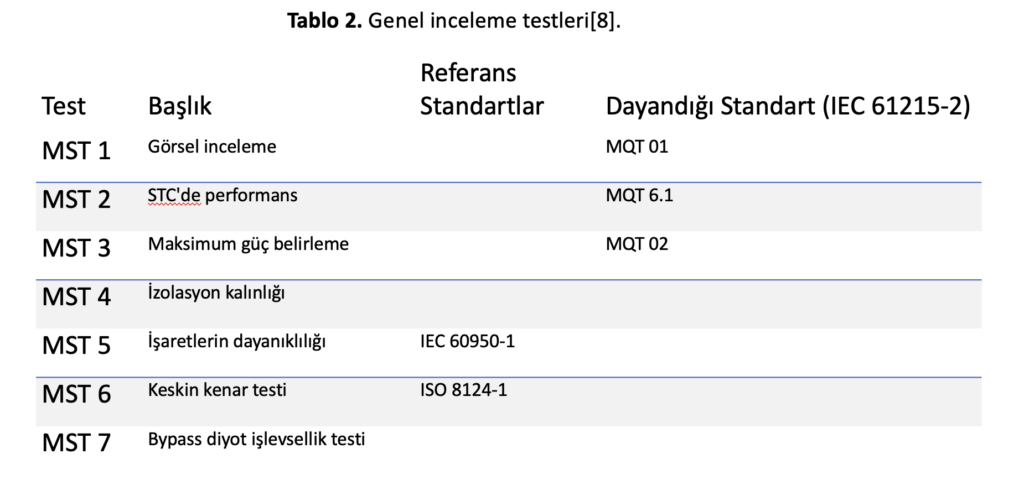
Las fábricas de paneles fotovoltaicos realizan varias combinaciones de todas las materias primas que se utilizarán en la producción de paneles junto con marcas alternativas. Estas combinaciones preparadas incluyendo todos los materiales y componentes especiales se incluyen en el Formulario de Datos Constructivos (CDF). Los paneles se fabrican de acuerdo con el CDF y a estos paneles se les aplican numerosas pruebas como la prueba de ciclo térmico, la prueba de congelación por humedad, la prueba de calor húmedo, la prueba de carga mecánica, tal y como exigen las normas IEC 61215/IEC61730. Paneles solares; Si supera con éxito las pruebas según las normas IEC 61215 e IEC 61730, tiene derecho a recibir un certificado. Después de esta etapa, los paneles tienen un CDF aprobado y certificados IEC 61215/IEC 61730 además del CDF. La fábrica produce los paneles de acuerdo con la lista de materiales denominada BOM List y esta BOM List debe incluir los materiales del CDF.
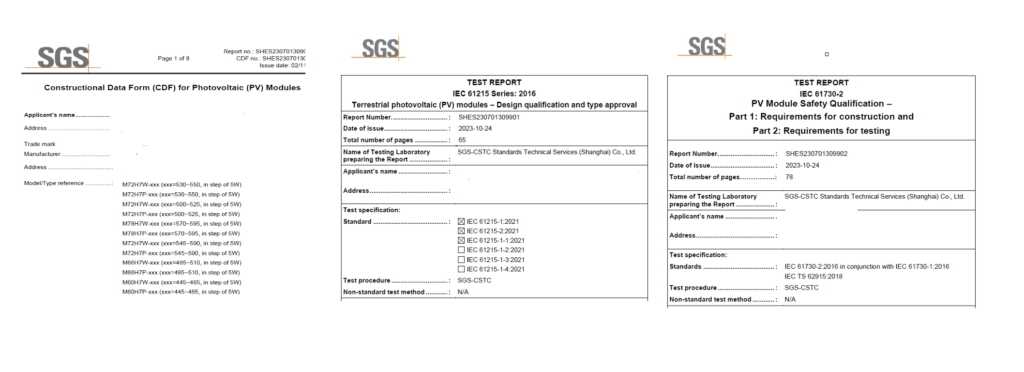
Pruebacelular
La prueba de células solares se aplica como primer proceso de la producción de paneles solares. Durante la prueba, se comprueba el rendimiento eléctrico de la célula bajo una simulación solar. Además, como prueba de calidad, se comprueban los efectos negativos no deseados, como la calidad de la superficie, las fracturas y las grietas [9]. La figura 5 muestra la máquina de corte de células.
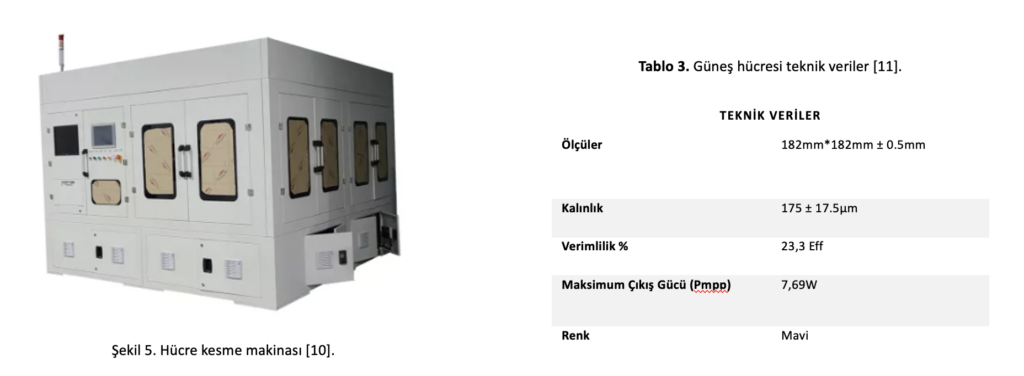
Carga de vidrio
Los vidrios utilizados en la producción de paneles solares son vidrios templados planos o esmerilados con bajo contenido en óxido de hierro. El bajo contenido en óxido de hierro aumenta la transmitancia luminosa del vidrio. En la línea de producción, los vidrios se cargan con precisión mediante brazos robotizados automáticos. La gran precisión de los brazos robotizados minimiza el riesgo de rotura y agrietamiento de los vidrios durante la carga. Una vez cargados los vidrios, se someten a procesos de control de superficie y limpieza. En esta fase se detectan las grietas y deformaciones de la superficie [9]. La figura 6 muestra el vidrio de un módulo fotovoltaico y la figura 7, la máquina de carga de vidrio de una fábrica de módulos fotovoltaicos.
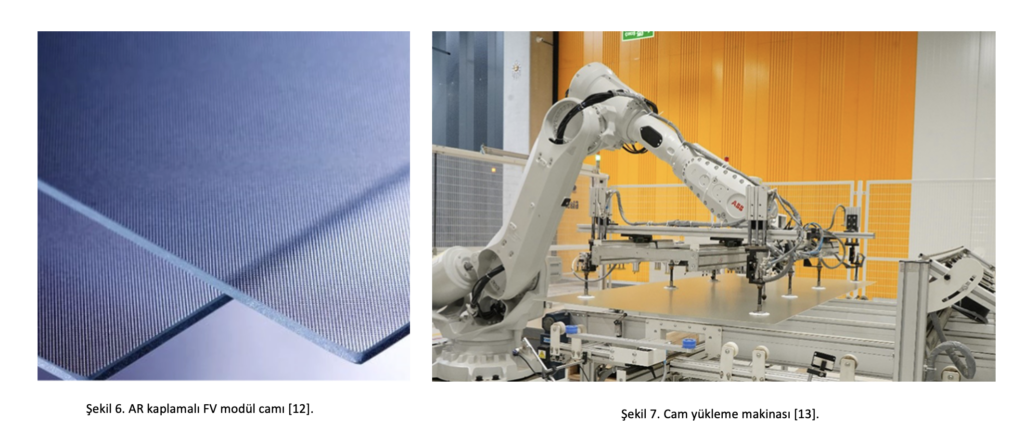
Línea de colocación de láminas
Las láminas solares de EVA (etilvinilacetato) se utilizan en los sistemas de producción de paneles solares para hacer más eficiente la generación de electricidad y proteger las células contra los impactos. En esta línea de producción, las láminas de EVA se combinan entre el vidrio y las células [9]. La figura 8 muestra la máquina de colocación de EVA.
El EVA es una capa especial y se sitúa entre el vidrio y las células, así como entre las células y la lámina posterior. El EVA aplicado en ambas caras se funde mediante el método de laminación en caliente y envuelve completamente las células solares. Este proceso aumenta la durabilidad del panel y evita que elementos como el agua y el micro polvo se filtren en su interior. También protege las células solares absorbiendo impactos y vibraciones[14].
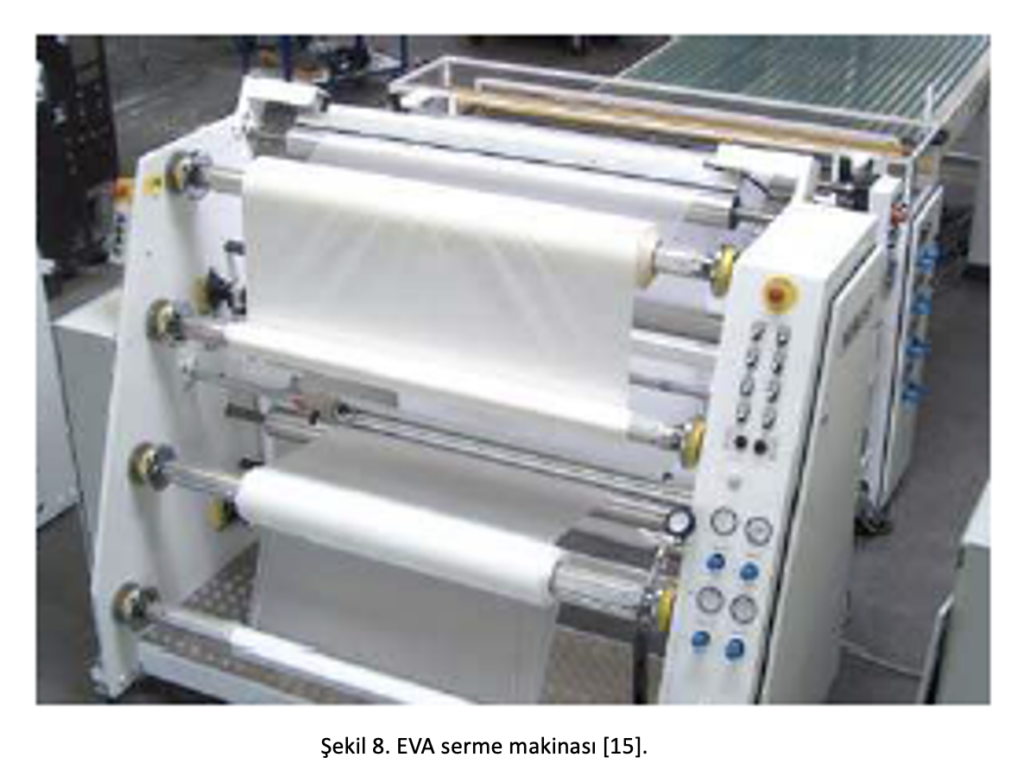
Stringer y línea de soldadura
Una vez detectadas las microfisuras y deformaciones en las células solares, éstas se alinean cuidadosamente en la línea de producción. Las máquinas stringer realizan el proceso de soldadura mediante infrarrojos o láser después de rociar pasta de soldadura sobre las células [9]. La figura 9 muestra la máquina stringer. En la máquina stringer se sueldan a las células unos hilos conductores denominados cinta. La figura 10 muestra una imagen del proceso de soldadura.
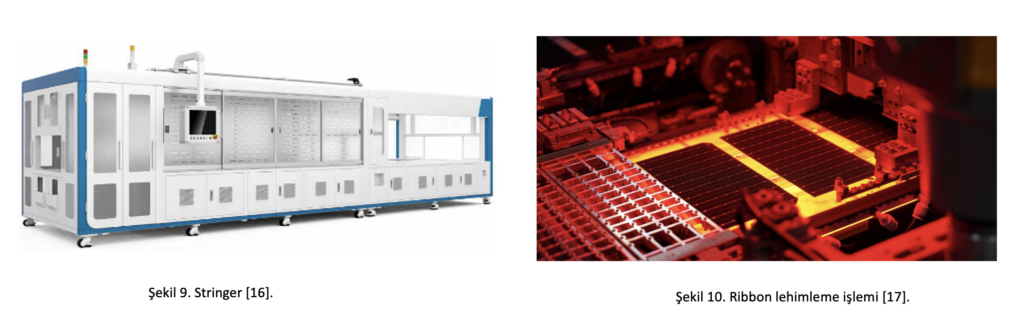
Línea de laminación
Una vez que el módulo fotovoltaico sale de la zona de stringer, se envía a la línea de laminación colocando de nuevo material EVA en la cara posterior y vidrio con recubrimiento AR o lámina posterior sobre él. Aquí, a alta temperatura y presión, todos los materiales se entrelazan y se convierten en un todo.
Las láminas posteriores son la capa exterior de los paneles solares y proporcionan el aislamiento eléctrico de los circuitos internos del entorno exterior. Esta capa desempeña un papel fundamental en la protección del panel frente a las duras condiciones ambientales. Aumenta la durabilidad de los paneles solares durante toda su vida útil y reduce el riesgo de seguridad [14]. La figura 11 muestra la lámina posterior utilizada para el módulo fotovoltaico. En la línea de laminación, el material EVA debe fundirse completamente a un tiempo y una temperatura constantes para obtener un aspecto transparente y agarrar muy bien las células y todo el panel [9]. La figura 12 muestra la línea de laminación.
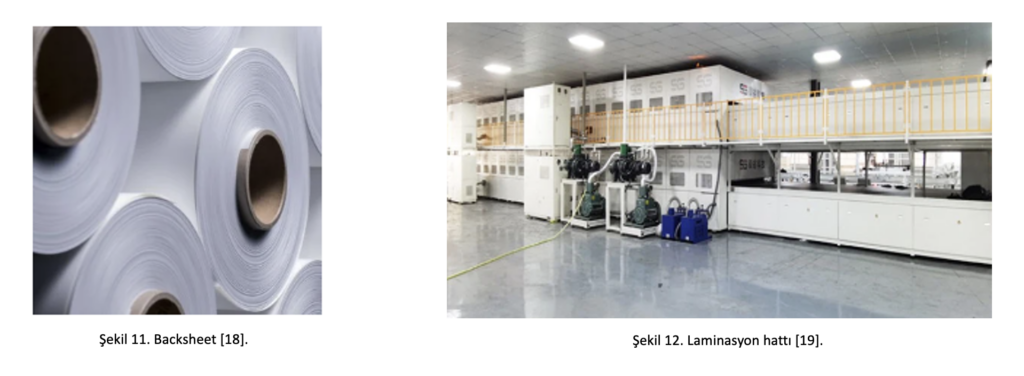
Línea deprensa
Una vez realizados el canteado y el corte de los paneles y los marcos, se envían a esta línea para el montaje del marco. Una vez terminado el proceso del marco, se monta la caja de conexiones en los paneles [9]. La figura 13 muestra la línea de prensado de marcos. Los marcos de aluminio utilizados en la producción de módulos fotovoltaicos son componentes importantes en los que deben tenerse en cuenta factores como el diseño adecuado de los orificios de montaje, los pesos establecidos, el grosor del revestimiento y las proporciones de los elementos en el contenido. El bajo contenido de hierro en los marcos de aluminio reduce el riesgo de corrosión y el revestimiento anodizado evita el deslustre [14]. El marco se muestra en la figura 14.
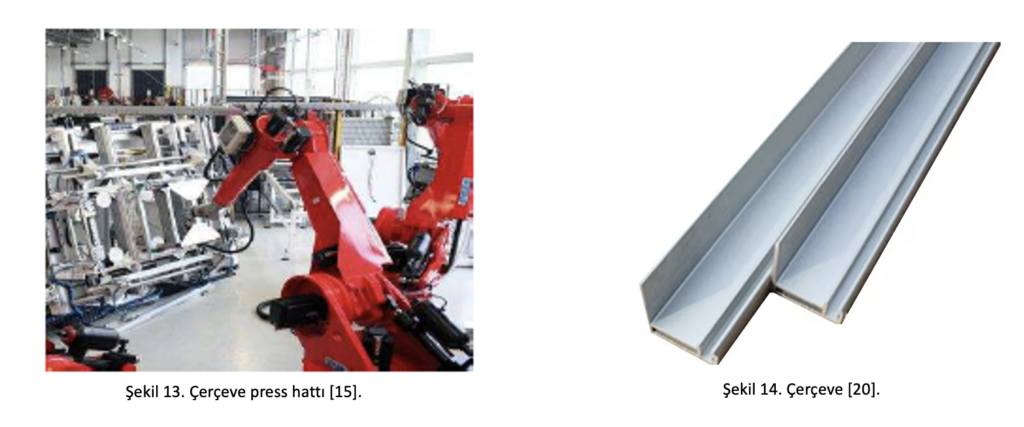
Conexión de la caja de conexiones
Una caja de conexiones se fija a los módulos que salen del marco. La caja de conexiones, que conecta las células de los paneles solares fotovoltaicos en serie entre sí, protege eléctricamente el panel transmitiendo la electricidad generada a las líneas externas. Los diodos de su interior proporcionan protección contra los rayos UV del sol. Al mismo tiempo, esta caja proporciona acceso para la detección y reparación de averías que puedan producirse en el panel [14]. La figura 15 muestra la caja de conexiones.
Los controles de materias primas realizados durante la auditoría de producción también deben llevarse a cabo para la lámina posterior, la caja de conexiones y el marco. El punto a considerar aquí es que los modelos de marca de estos productos están incluidos en el CDF. Si consideramos esta cuestión especialmente para la caja de empalmes, hay tres aspectos que deben comprobarse. Se trata de la derivación, el cable y el conector. Estos tres elementos forman la caja de empalmes. Cada marca de caja de empalmes puede utilizar diferentes productos para estos tres elementos. Por ejemplo, un diodo de derivación codificado como 4045 se utiliza en una caja de empalmes con una corriente nominal de 25 A, mientras que el 5045 puede utilizarse para 30 A. Estas combinaciones también deben cumplir la CDF.
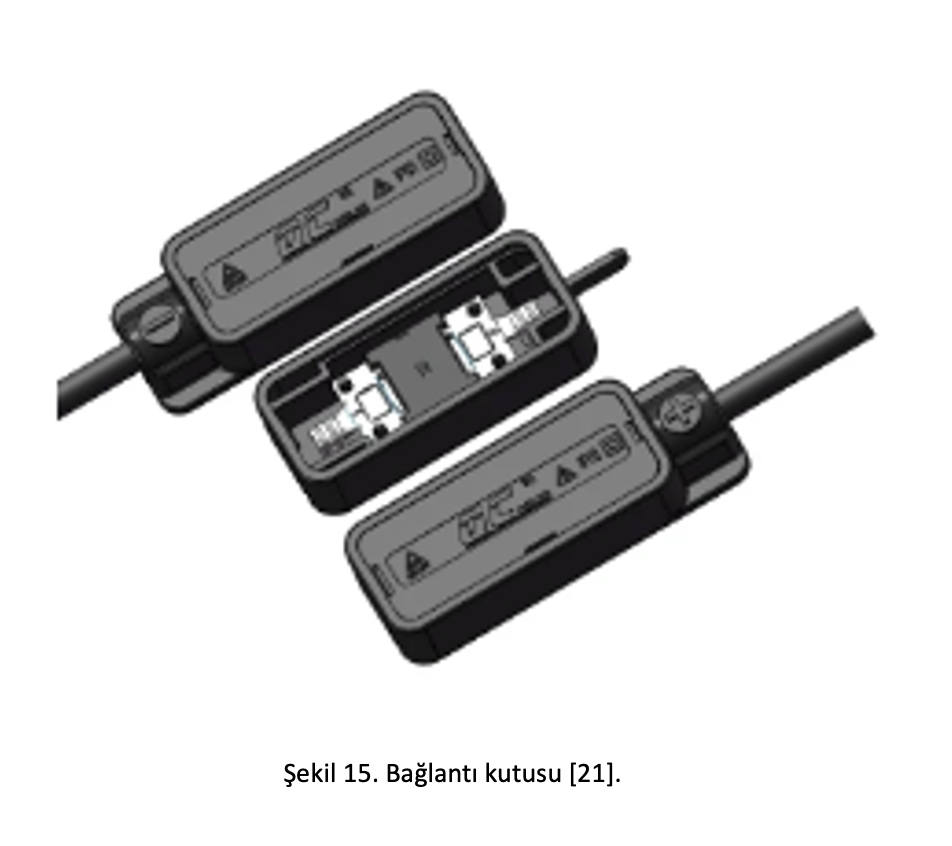
Pruebas aplicadas en el ámbito de la CEI 61215/CEI 61730
Inspecciónvisual
Los módulos fotovoltaicos se inspeccionan en las siguientes condiciones bajo una iluminación no inferior a 1000 lux.
-Superficies exteriores agrietadas, alabeadas, desalineadas o desgarradas.
-Células rotas y agrietadas,
-Puntos de conexión o juntas defectuosas,
-Células en contacto entre sí o con el marco,
-Desorden de las uniones adhesivas,
-Un camino continuo entre una célula y el borde del módulo, formado por burbujas o pliegues,
-Superficies adheridas de materiales plásticos,
-Terminaciones defectuosas expuestas a partes eléctricas bajo tensión,
-Todas las demás condiciones que puedan afectar al rendimiento [22].
Las imágenes de electroluminiscencia (EL) de los módulos fotovoltaicos se analizan para detectar microfracturas que no son visibles a simple vista.
Las imágenes de electroluminiscencia suelen obtenerse en entornos poco iluminados y suelen ser en escala de grises. Los defectos en dichas imágenes suelen aparecer en regiones oscuras; en concreto, las fracturas y otros defectos aparecen como líneas negras o manchas oscuras. Las imágenes de electroluminiscencia son un método de detección de defectos muy utilizado en muchas empresas de fabricación [23]. La figura 16 muestra la imagen EL del módulo fotovoltaico.
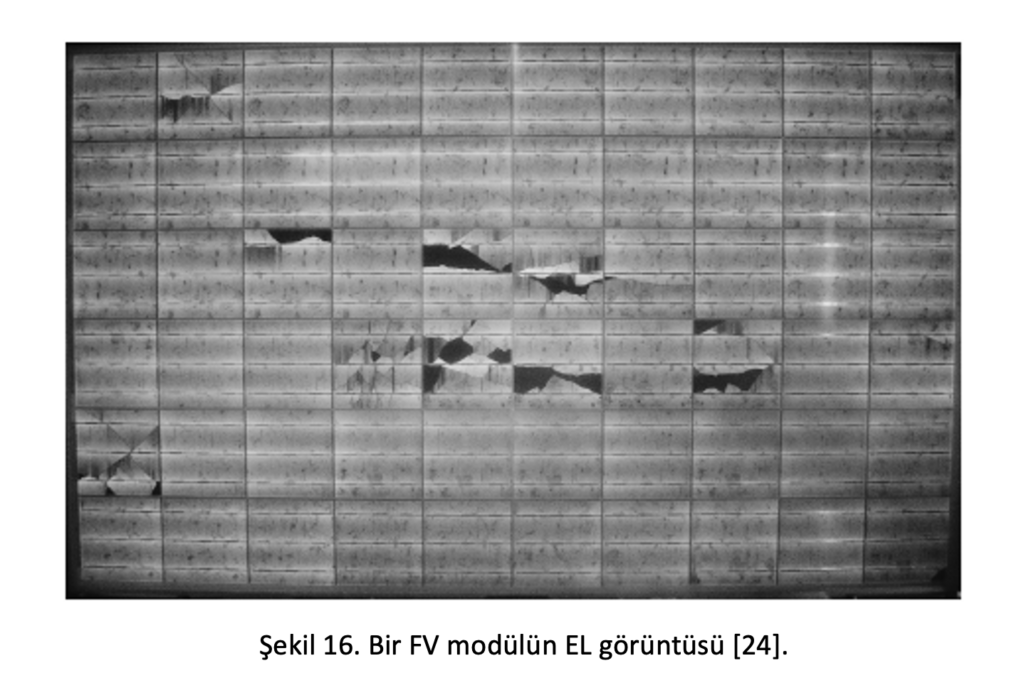
Determinación de la potencia máxima ( Determinación de lapotenciamáxima )
La potencia del módulo fotovoltaico se determina con una irradiancia de 1000W/m² y una temperatura de 25°C[22].
Prueba deaislamiento
Esta prueba determina si existe un buen aislamiento entre las partes conductoras de corriente del módulo y el marco o el entorno. La resistencia de aislamiento de los módulos con una superficie inferior a 0,1m2 no deberá ser inferior a 400 MΩ. Para los módulos con una superficie superior a 0,1m2, el valor de la resistencia de aislamiento medida a 500 V o a la tensión máxima del sistema, la que sea mayor, multiplicado por la superficie del módulo no deberá ser inferior a 400 MΩ xm2 [22]. La figura 17 muestra el armario de pruebas de aislamiento TSE.
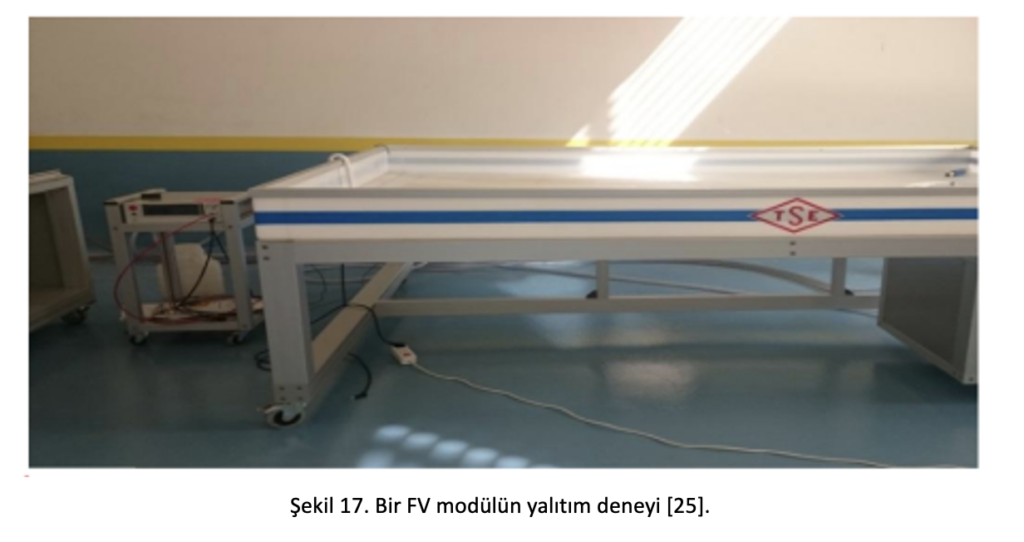
Medición de los coeficientes detemperatura
La potencia de las células monocristalinas y policristalinas con tecnología de cristal disminuye al aumentar la temperatura. El bajo coeficiente de temperatura reduce la pérdida de energía cuando aumenta la temperatura. Cuando el módulo alcanza la temperatura deseada, se midenel ISC, el VOC y la potencia máxima. La temperatura del módulo se modifica en pasos de unos 5°C en el intervalo de interés de al menos 30°C y se repiten las mediciones deISC, VOC y potencia pico [22]. La figura 18 muestra el experimento relacionado.
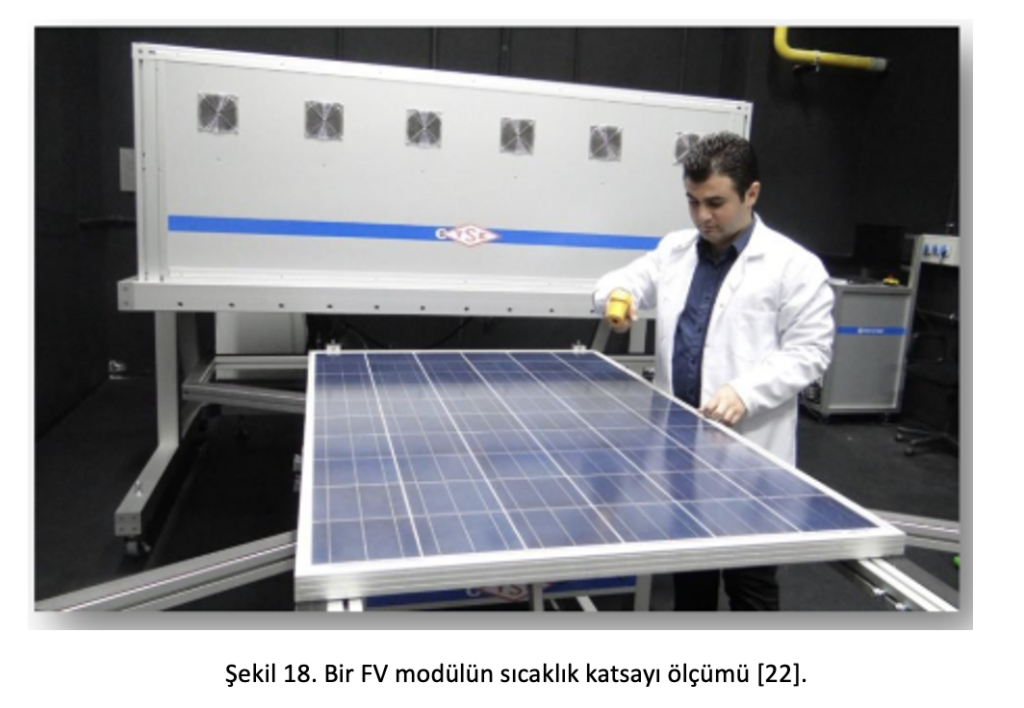
Prueba de resistenciaen caliente
El objetivo de este experimento es determinar la capacidad del módulo para soportar efectos de calentamiento por puntos calientes, por ejemplo, la fusión de la soldadura o la distorsión de la carcasa pueden crear un efecto de calentamiento. Este defecto también puede verse potenciado por células agrietadas o desajustadas, defectos de interconexión, efecto fantasma parcial o manchas. No debe haber defectos visibles, la reducción de la potencia máxima de salida no debe superar el 5% del valor medido antes de la prueba y la resistencia de aislamiento debe cumplir las mediciones iniciales[22].
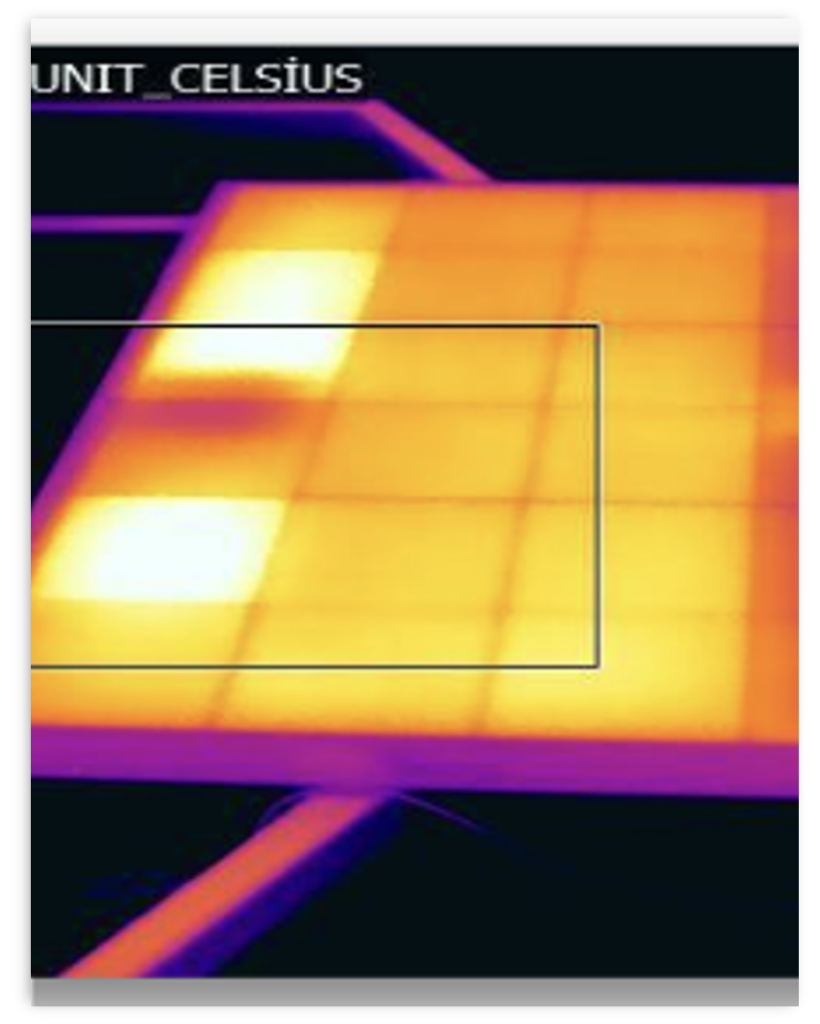
Prueba de preacondicionamientoultravioleta
El módulo fotovoltaico se preacondiciona con radiación ultravioleta (UV) para identificar los materiales y los aglutinantes adhesivos sensibles a la degradación UV antes de los experimentos de ciclos térmicos/congelación por humedad. La temperatura del módulo es de 60 ºC ± 5 ºC cuando se irradia con luz UV, con un rango de longitud de onda entre 280 nm y 385 nm, con una banda de longitud de onda total de 15 kWh/m2.[22].
Prueba de ciclado térmico (Thermal Cycling Test)
Se determina la capacidad del módulo fotovoltaico para soportar el desajuste térmico, la fatiga y otras tensiones causadas por los cambios repetidos de temperatura. Se aplican 50 y 200 ciclos en el rango de -40 °C a +85 °C. Durante el experimento, no debe haber interrupción del flujo de corriente[22].
Prueba dehumedad-congelación
Determina la capacidad del módulo fotovoltaico para resistir los efectos de las altas temperaturas y la humedad tras temperaturas bajo cero. No se trata de una prueba de choque térmico. Se aplican 10 ciclos a +85 °C y -40 °C, 85% HR de humedad relativa [22].
Prueba decalor húmedo
Determina la capacidad del módulo fotovoltaico para soportar la humedad y los efectos de penetración a largo plazo. Se aplica una prueba de 1000 horas, +85 °C, 85% HR de humedad relativa[22].
Pruebade corriente defuga húmeda (Wet Leakage Current Test)
Esta prueba evalúa el aislamiento del módulo fotovoltaico en condiciones de funcionamiento húmedas y verifica que la humedad de la lluvia, la niebla, el rocío o la nieve derretida no penetra en las partes activas del circuito del módulo causando corrosión, fallos a tierra o riesgos para la seguridad[22].
-Resistencia: 3.500Ω o inferior
-Tensión superficial: 0,03 N/m o menos
-Temperatura: 22 ºC ± 3 ºC
Para los módulos con una superficie inferior a -0,1 m², la resistencia del aislamiento no debe ser inferior a 400 MΩ. Para los módulos con una superficie superior a 0,1 m², la resistencia de aislamiento medida multiplicada por la superficie del módulo no debe ser inferior a 40 MΩ.m² [22].
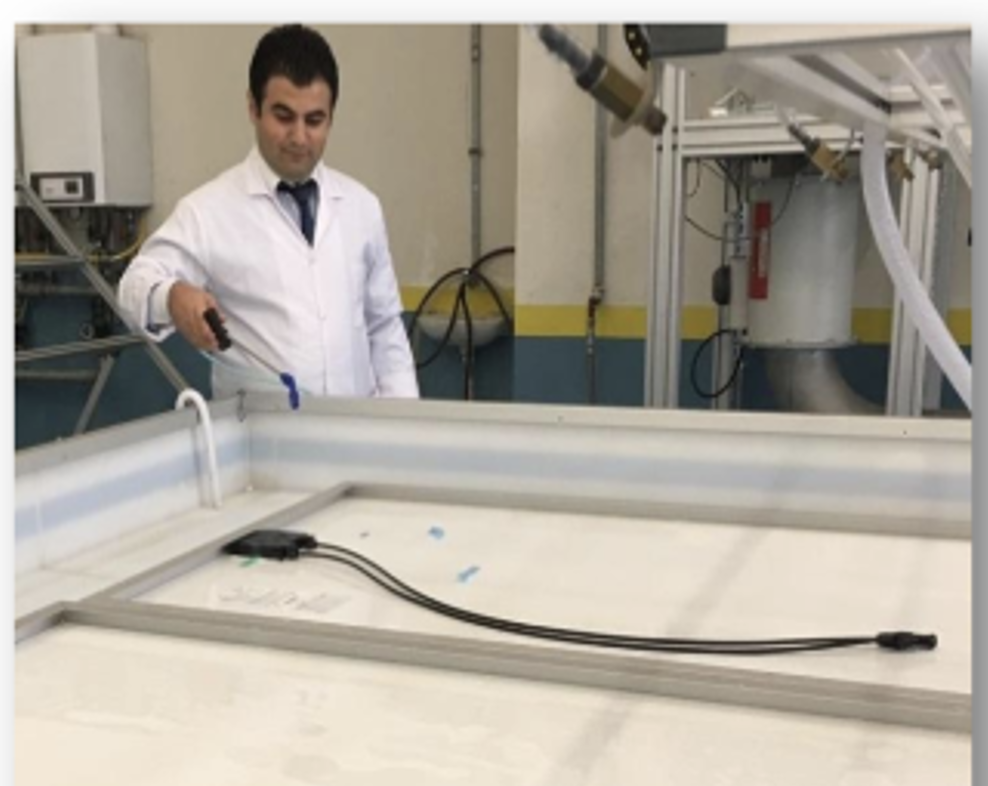
Prueba de cargamecánica( Prueba decargamecánica )
El objetivo de este experimento es determinar la resistencia de un módulo fotovoltaico (FV) al viento, la tierra, las cargas estáticas o las cargas de hielo. Durante el experimento, el módulo se alimenta para controlar continuamente la integridad eléctrica de los circuitos internos del módulo. Se aplica una carga de 2400 Pa a su superficie delantera y trasera durante 1 hora en tres ciclos[22].
Se consideran 2400 Pa como referencia para vientos fuertes con un factor de seguridad de 3 y una velocidad de 130 km/h (aproximadamente ± 800 Pa). Si se requiere que el módulo soporte grandes acumulaciones de nieve o hielo, la fuerza que debe aplicarse a la superficie frontal del módulo se incrementa de 2400 Pa a 5400 Pa para el último ciclo. Durante la prueba, no debe detectarse un fallo continuo de circuito abierto y no debe haber defectos visibles importantes. Además, la reducción de la potencia máxima de salida no debe superar el 5% del valor medido antes del experimento [22].
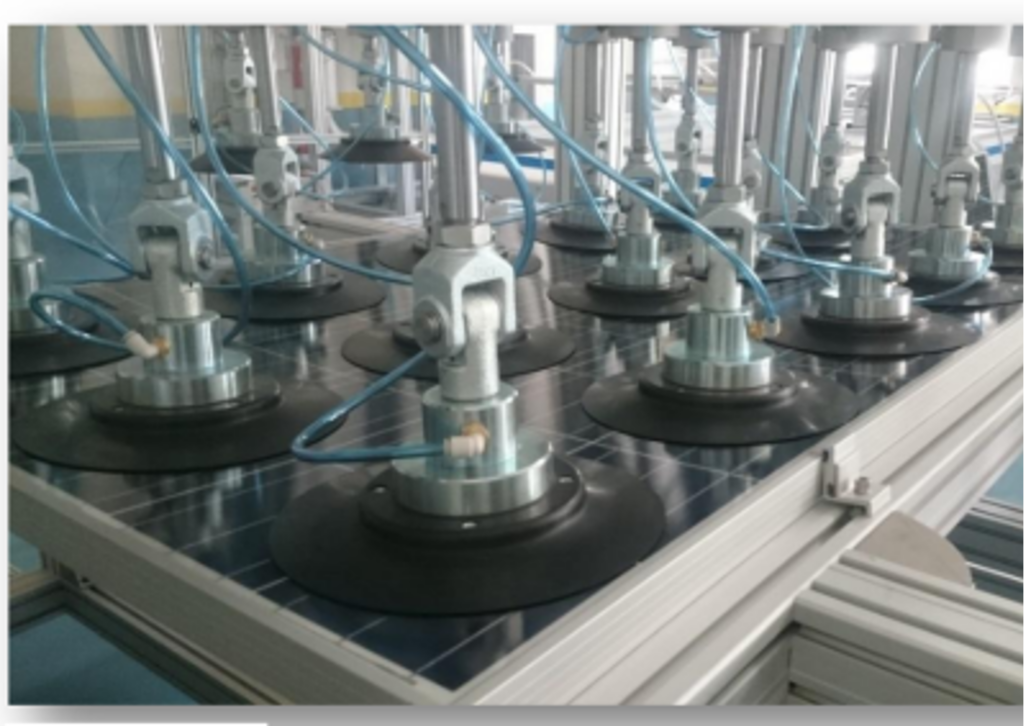
Imágenes de electroluminiscencia (EL)
La detección precoz de defectos en los paneles fotovoltaicos es fundamental para garantizar la eficiencia, fiabilidad y longevidad de los sistemas. Los defectos pueden reducir la eficiencia de los paneles, limitar la producción de energía y plantear riesgos para la seguridad. Estas detecciones se realizan mediante métodos como la inspección visual, las pruebas eléctricas y la supervisión del rendimiento, y corren a cargo de equipos especializados. En particular, las imágenes de electroluminiscencia (EL) se utilizan ampliamente como método para resaltar fracturas y otros defectos en los paneles. Los dispositivos EL detectan los defectos captando la radiación generada por la corriente continua aplicada a los paneles con cámaras especiales. Este proceso es necesario para mejorar el rendimiento y la vida útil de los paneles durante las fases de producción y explotación y debe cumplir la normativa local. La detección y eliminación de defectos garantiza un rendimiento óptimo del sistema, reduciendo los costes de funcionamiento y aumentando los beneficios medioambientales [23].

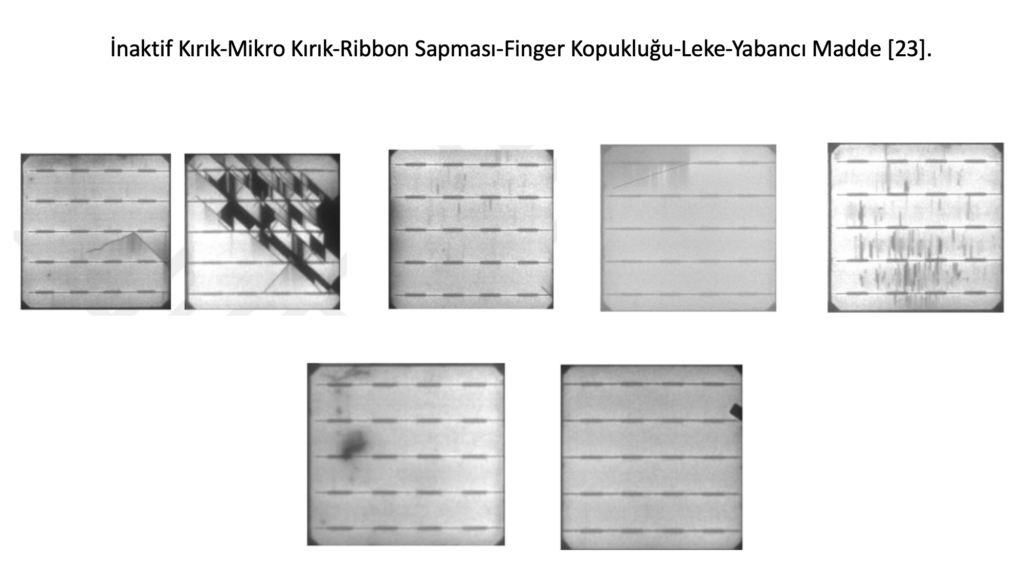
Autor:
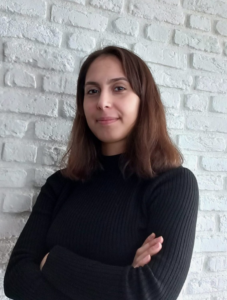
Melisa Ekşi